Non-compliance with Standard Operating Procedures (SOPs) is a critical issue in industries such as chemical processing, oil and gas, pharmaceutical manufacturing, and healthcare. Traditionally, non-compliance has been viewed negatively, as it is seen as deviating from the intended ways in which a task should be performed. This is particularly the case for safety critical tasks, where a non-compliance is seen as subverting the systems and barriers which have been designed to manage identified risks when the system was designed. Non-compliance is often attributed to people prioritising individual or team benefits such as getting a job done quickly rather than minimising risks.
While the traditional approach has been to attribute non-compliance to operator shortcomings, a deeper analysis reveals that in fact, non-compliance may actually provide benefits such as greater efficiency and reduced likelihood of human errors giving rise to unwanted. Thus, understanding the nature of non-compliance can reveal deeper systemic challenges and opportunities for improvement. Here, we explore the root causes of non-compliance and strategies for creating more effective procedures.
Understanding the distinctions between Violation, Non-compliance, Workaround, and Innovation is crucial. Each term refers to a different way of deviating from established procedures or norms, with unique causes, implications, and potential benefits or risks.
Violations | Non-compliance | Workarounds | Innovations | |
---|---|---|---|---|
Definition | Intentional deviations from established procedures, rules, or guidelines. | Failure to adhere to a procedure, standard, or regulation, either intentionally or unintentionally. | Informal methods developed by workers to achieve a task or goal outside the documented procedure. | Deliberate and often positive changes to improve processes, developed through operator experience or new insights. |
Nature | Often deliberate but not always malicious; can be motivated by a desire to improve efficiency or deal with perceived inadequacies in the procedures. May also stem from complacency or risk-taking behaviour. | Broader than violations; includes both accidental oversights and deliberate decisions not to comply. Often arises from systemic issues, such as unclear instructions, lack of training, or resource constraints. | Typically, unapproved but often practical solutions to address real-world challenges not accounted for in the official SOPs. Can reflect ingenuity and problem-solving but may also introduce risks. | A step beyond workarounds, innovations are intentional improvements that could enhance safety, efficiency, or productivity. May involve proposing and formalising changes to existing procedures. |
Example | An operator ignoring a safety step because they believe it’s unnecessary or too time-consuming. | An operator skipping a step in the process due to unclear instructions or lack of awareness of its importance. | Using a personal method to speed up a process or handle equipment limitations more effectively. | Designing a new tool or method to perform a task more safely or effectively. |
Implication | Potentially dangerous, as it bypasses established safety or operational measures. May result in disciplinary actions if the violation leads to adverse outcomes. | Indicates potential weaknesses in the system, such as poorly designed SOPs or insufficient risk awareness. Addressing non-compliance often requires improving procedures or providing better training. | Can be beneficial if they improve efficiency or safety, but harmful if they undermine safety protocols or lead to unexpected outcomes. Highlight a need for procedure review to integrate useful workarounds officially. | Can significantly benefit operations if recognized and adopted formally. Encourages a culture of continuous improvement when supported by the organisation. |
The Reality of Procedural Compliance
Procedures are intended to document the safest and most efficient ways to operate processes, often developed by engineering teams during commissioning. However, real-world scenarios frequently reveal a gap between Work as Imagined by the engineering designers of the system, and Work as Done at the shop floor level. This disconnect often leads operators to develop informal workarounds, sometimes out of necessity.
Why Do Operators Deviate from SOPs?
Several factors contribute to procedural non-compliance, including:
- Complexity and Usability Issues
Procedures are often lengthy, technical, and difficult to follow, especially under pressure. They are often written from a purely engineering perspective, which may be out of touch of operating realities, or important issues such as the usability of the equipment provided to perform the tasks. Also, assumptions are made regarding the number of staff available to perform the task which may be compromised by holidays or sickness. They may not account for varying levels of operator expertise, leaving experienced personnel overwhelmed with unnecessary details.
- Risk Awareness and Perception
Operators may become habituated to risks, especially when workarounds appear to have no immediate negative consequences. Critical steps in procedures may not highlight the potential severity of outcomes of failure.
- Disparity Between Documentation and Reality
Procedures developed without sufficient input from operators often fail to reflect real-world tasks, leading to informal adaptations. Changes in operations over time can make older SOPs outdated, requiring ad hoc improvisation.
- Challenges with Checks and Verifications
Operators may skip checks perceived as low-value or burdensome. This is particularly the case where the consequences of non-compliance are seen as low, where compliance is perceived as effortful, time consuming and mainly performed to satisfy bureaucratic norms.
It is often assumed that double checking by a second operator will correct any non-compliance. However, it is extremely difficult to ensure that checkers maintain their independence, particularly when they rarely find any errors or non-compliance. Time pressures and resource constraints can also impede independent verifications as they are seen to produce few benefits.
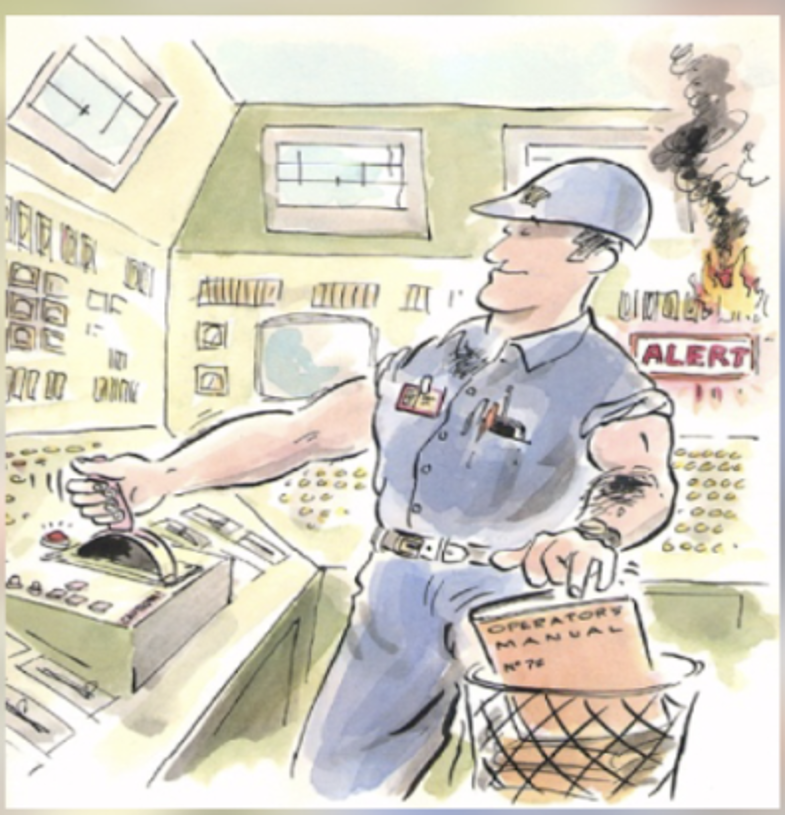
Addressing Non-Compliance: Common Mistakes
Traditional responses to procedural violations—such as blaming operators, retraining, or increasing supervision—often fail to address the root causes. These approaches can foster a culture of silence and resistance, where operators feel discouraged from sharing insights into operational realities which make it impossible to perform tasks in the prescribed manner.
The SHERPA approach to Enhancing SOP Compliance
SHERPA (Systematic Human Error Reduction in Process Analysis) is a comprehensive platform for reducing the risks arising from human error. It was originally developed in the context of risk analyses of safety critical tasks in oil and gas, healthcare, transport and other high-risk industries. It is also known as SCTA (Safety Critical Task Analysis). It offers a structured methodology to address procedural non-compliance by integrating task analysis, error identification, and training:
- Improving Procedure Usability
Procedures are reorganized using Hierarchical Task Analysis, breaking them into logical subtasks. Error analysis is used to highlight potential failure points, ensuring these are explicitly addressed in training and included in SOPs to indicate where potential errors leading to serious consequences may be more likely.
- Capturing tacit knowledge
Tacit knowledge refers to undocumented insights that operators gain from working with a system, which is often the basis for innovations and improvements, even though these may technically be violations. Eliciting this knowledge requires an open forum where both innovations and non-compliance are openly discussed, and if they improve on current SOPs, are distributed across the workface. This is one of the main requirements of a learning organisation. Participants gain a deeper understanding of tasks and their associated risks, fostering more informed decision-making. The use of this collaborative procedure development process encourages ownership and commitment among SOP users.
Conclusion
Non-compliance is rarely a simple matter of operator negligence. By understanding the systemic causes and incorporating operator feedback into procedure development, organizations can create a culture of safety, efficiency, and continuous improvement. Tools such as SHERPA not only reduce non-compliance but also foster collaboration, knowledge sharing, and operational excellence.
While violations and non-compliances point to potential weaknesses in adherence or system design, workarounds and innovations offer opportunities for learning and improvement. Organizations should therefore strive to understand why deviations occur and foster a culture where beneficial practices are identified, supported, and formalized. This approach helps strike a balance between compliance, safety, and efficiency.
Get in touch with us today by emailing [email protected] to see how SHERPA can improve compliance within your organisation.
Our colleague, Dominic, discusses the challenges of implementing checks and how solutions from a systemic level could improve such challenges. Visit his blog here to find out some examples of good checking practices here.