In my last blog post, I explained the steps in the Human Factors (HF) Roadmap, which serve as a structure for integrating sustainable human factors management across COMAH establishments. Based on the HSE’s Seven Steps Approach in managing human failure, the roadmap illustrates how human factors risk assessment can mitigate the chances of Major Hazard Accidents (MAH) scenarios at such sites.
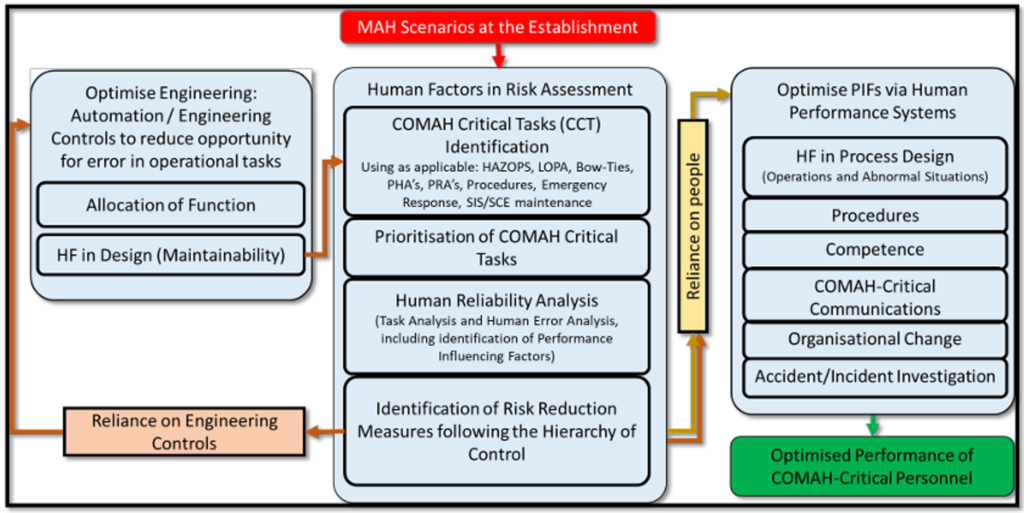
In this blog, I will demonstrate how Safety Critical Task Analysis (SCTA), as a methodology, maps onto the HF Roadmap as an example of its implementation in practice. We will look at where the rubber meets the road – the point at which a theory is put to a practical test.
The SCTA workflow offers a simplified view of the tasks that need to be performed to complete an SCTA study.
Understanding the Safety Critical Task Analysis (SCTA) process?
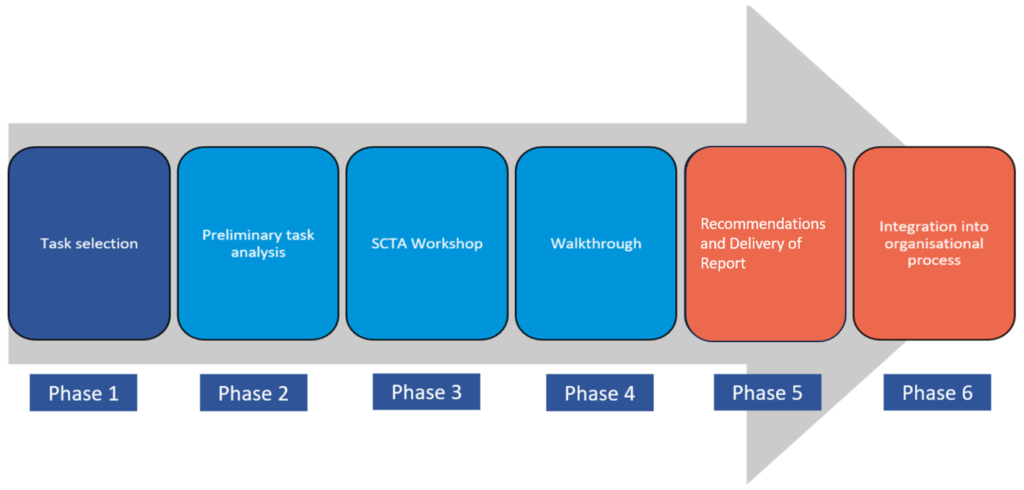
Safety Critical Task Analysis (SCTA) is a methodology used to help organisations manage Human Performance at their sites. The origins of the method can be traced back to Systemic Human Error Reduction and Prevention Analysis (SHERPA), which was first devised by our Managing Director, David Embrey. This influenced the approach used in the HSE Offshore Technology Report, OTO 1999/092, and laid the foundations for what we call SCTA today. The SCTA process goes by other various names, including Human Factors Critical Task Analysis (HFCTR), Human Factors Critical Task Analysis (HFCTA) and SYSTEMS Critical Task Analysis (SCTA).
The SCTA workflow consists of six phases (Figure 1).
- Task Selection
- Preliminary Task Analysis
- SCTA Workshop
- Walkthroughs
- Recommendations and Delivery of Reports
- Integration into the Organisational Process.
Phase 1: Task Selection
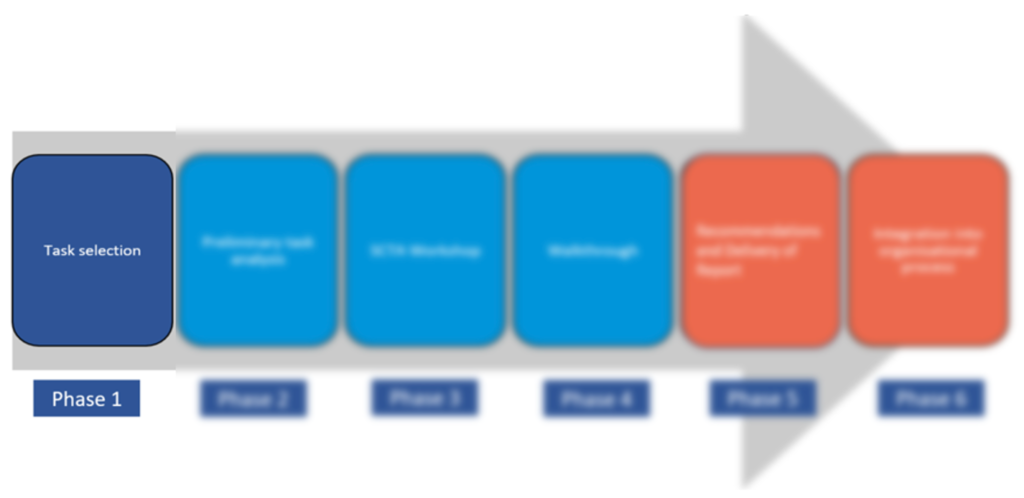
Similar to the HF Roadmap, the first phase in an SCTA study consists of selecting the appropriate tasks for assessment. In this phase we define the potential MAHs that could occur on the site and list the tasks associated with these MAHs. This list is created through insights from previous incidents or near misses, conversations with subject matter experts and frontline staff, and outputs from tools like Bow-Ties Diagram and HAZOPs.
Once the list has been established, we narrow the list of critical tasks to analyse by going through a prioritisation process. These tasks are ranked based on relevant criteria such as the severity of consequences, the likelihood of error, and the extent of human involvement in the task. The idea is that tasks with the most severe consequences and a high degree of human involvement will be ranked at the top of the list, and the severity of these factors reduces the further you go down the list. This prioritisation process is important for the SCTA workflow because it helps build an understanding of the critical tasks on-site and guides the order of the tasks to be analysed.
Phases 2 – 4: Human Reliability Assessment
Following task selection, we can start the human reliability assessment. This comprises a Preliminary Task Analysis, SCTA Workshop, and Walkthrough, or Phases 2 – 4 in the SCTA workflow.
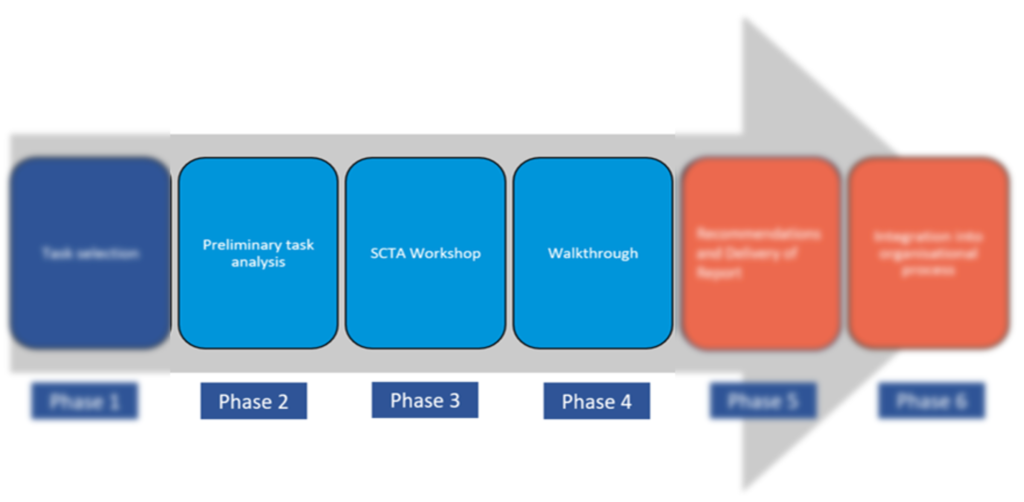
Phase 2: Preliminary Task Analysis
We start the risk analysis with a preliminary task analysis, also known as a Hierarchical Task Analysis (HTA). This provides a comprehensive understanding of the task at a step-by-step level. This can be created from scratch or by importing existing Standard Operating Procedures (SOPs). Representing the task as an HTA provides the ability to organise the many steps into discrete sections and subsections that make up the overall goal. This helps make complex tasks easier to understand. Engaging with lots of detail in a graphical form provides the opportunity to highlight discrepancies within the procedure.
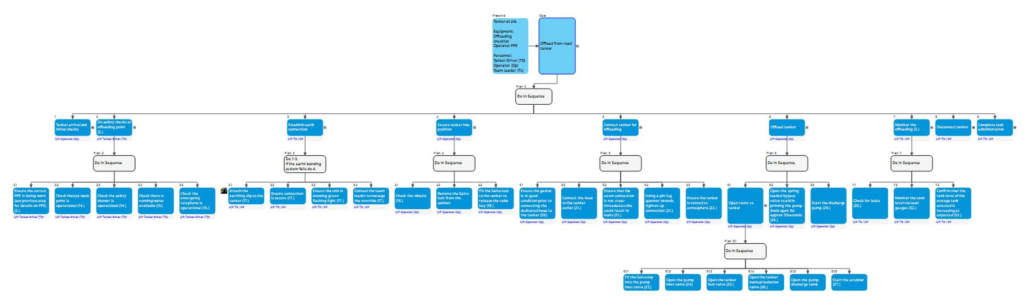
Phase 3: Workshop
Once the HTA is complete, we will organise a workshop with the people at the sharp end and the relevant subject matter experts. During the workshop, we will review the HTA with the workshop team to confirm the HTA is representative of what happens on-site. Often, we find that SOPs may not represent how the work is truly conducted by the operators, and these workshops are a great opportunity to address any discrepancies.
We also utilise the workshop to discuss the potential human errors that may contribute to a MAH scenario. This is known as the Failure Mode analysis. These could be errors like action omitted, checking incomplete, and information not communicated completely. At the same time, we also evaluate the contextual factors, or Performance Influencing Factors (PIF), that affect the likelihood of such errors occurring. These might be job factors (task complexity, task design), organisational factors (safety culture, training), or environmental factors (lighting, heating). These PIFs could either be positive or negative.
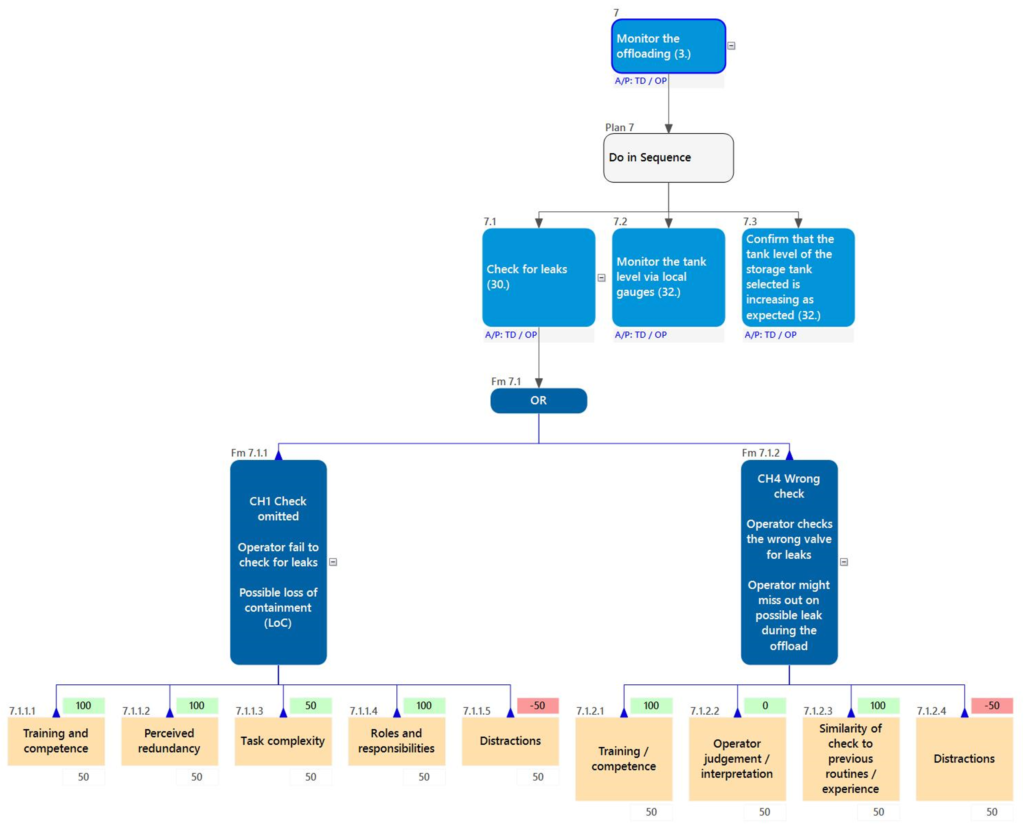
It is important that we gather the right participants for these sessions, such as experienced operators, process safety engineers, and instrument technicians (for Maintenance, Inspection, and Testing (MIT) tasks). Often, the workshops are where we elicit valuable information regarding potential issues that affect the task and establish the severity of their influences. By having the right people in the room sharing their knowledge and experience we ensure that the analysis addresses these issues and concerns.
Phase 4: Walkthrough
We complement the workshop by conducting a walkthrough of the task to gain further insights from frontline staff. This helps build a comprehensive picture of the operators’ working environment and allows us to identify additional situational and environmental challenges in completing the task. The walkthrough can be conducted before, during, or after the workshop to complement its findings and identify additional PIFs.
Phase 5: Recommendations and Delivery of Report
Now that the workshop and walkthroughs have been completed, we can start writing up the analysis report and the possible recommendations for improving the task. This parallels identifying the Risk Control Measures following the Hierarchy of Control in the HF Roadmap.
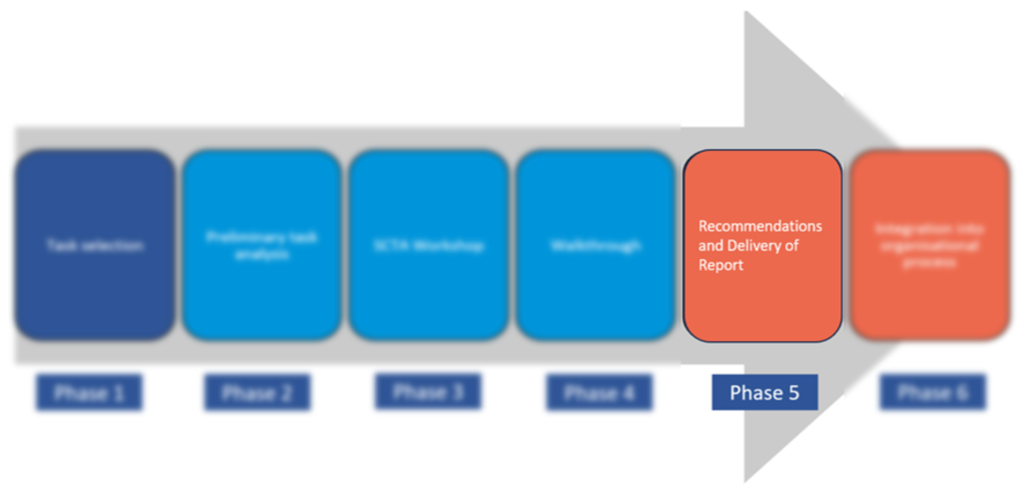
When writing the report, we want to outline the site’s efficacy in preventing potential MAH scenarios by evaluating the Risk Control Measures (RCMs) present at their site. RCMs range from engineering controls (trips and alarms) to the human element (reliance on operator checks). When evaluating these measures, we assess whether the controls protect against the types of human failures we have identified to be contributory to a MAH. If they are inadequate, then recommendations with reference to the hierarchy of control is required. This means that where there are MAH concerns with less efficient RCMs in place, we need to think about ways to eliminate the risks. If this is impractical, we move a level down the Hierarchy of Control and consider substituting or implementing further engineering controls to reduce the risks. At the same time, we will also recommend solutions to optimise any negative PIFs raised during the workshop. We should also use this opportunity to consider the positive PIFs on site and implement the good practices identified across other parts of the site.
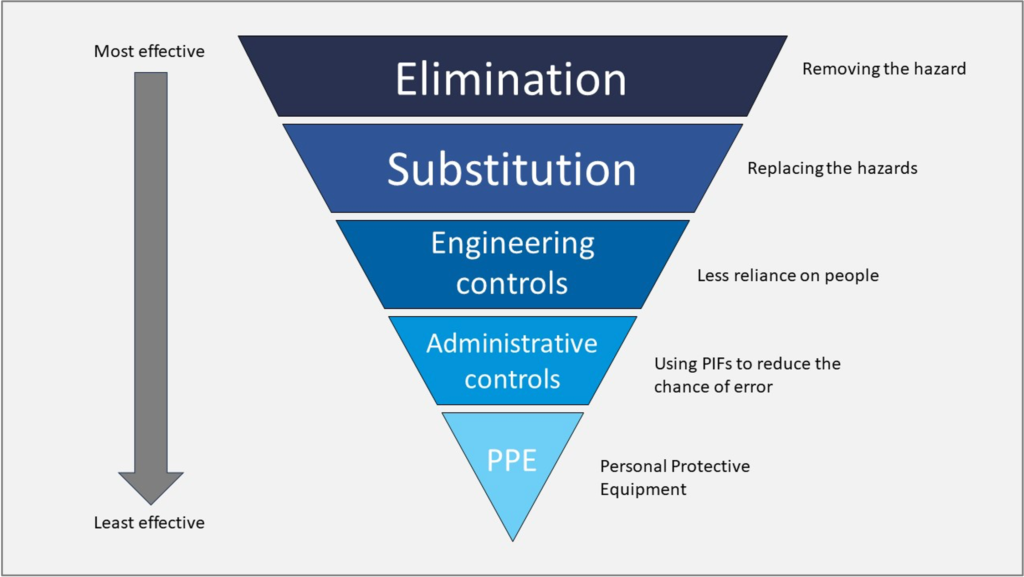
We have found that the starting point for discussing the recommendations and improvements should begin during workshops and walkthrough sessions rather than only after them. This is because they are opportune moments to determine the feasibility and practicality of implementing the possible improvements with the site personnel.
Phase 6: Integration into Organisational Processes
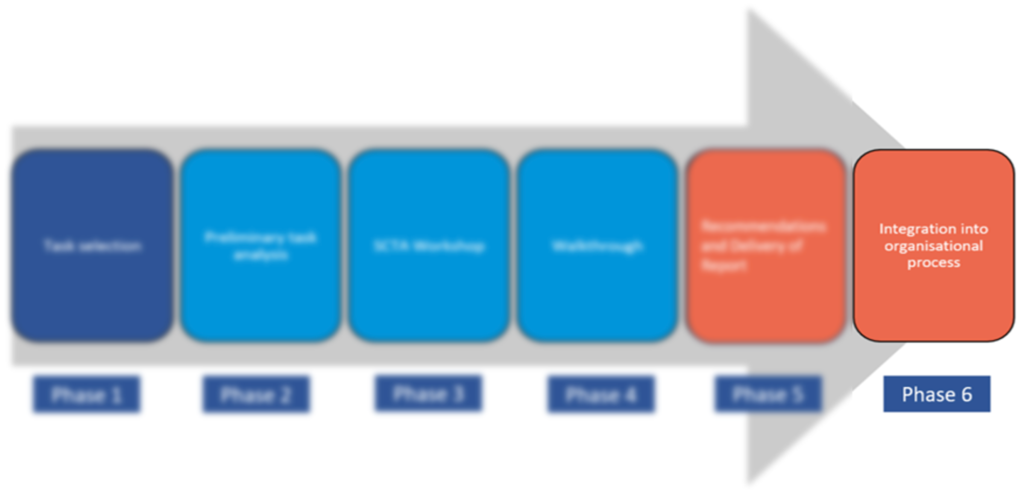
Once the report is complete, we move on to the final phase of the SCTA process – integrating the findings and outputs into the organisational process. By this stage, the SCTA analysis and report should have highlighted any engineering issues or PIFs that should be improved. We can then take these findings and implement them on the site. If the PIFs for the task have a negative influence on the task, then we can set out to optimise these PIFs, e.g. this could be by improving the job aids, valve labelling, gauge indication and position, access, ergonomics, task design, checks, key control and supervision, etc.
Review of the task details throughout the SCTA process can also provide updated information for a new draft procedure, and identification and assessment of critical steps means that these can be risk-informed procedures. To complement this, new competence standards based on the SCTA learnings can also be drafted so the knowledge and skill requirements are detailed for critical task steps to inform training design or updates. Other PIF areas for optimisation could include process design, critical communication, workload and staffing at the site.
Summary
In the previous blog, I reviewed the HF Roadmap, which outlines how COMAH sites can manage human factors and performance. In this blog, I showcased how the SCTA process could be used to implement the HF Roadmap in practice. Each of the phases in the SCTA process aligns nicely with the HF Roadmap, thus making SCTA a practical tool for managing human factors risk assessment at their site.
Whether you want to enhance your grasp of the HF Roadmap or embark on the journey of conducting SCTAs, our courses cater to your specific learning needs.
If you’re eager to deepen your understanding of the HF Roadmap and the HF Delivery Guide, our HF_PLC course presents an excellent opportunity. This course is tailored to provide comprehensive insights into the intricacies of human factors management within COMAH establishments.
If you’re keen on mastering the art of conducting Safety Critical Task Analyses (SCTAs), our flagship SCTA course offers a robust foundation, equipping you with the skills and knowledge necessary to navigate the complexities of SCTAs effectively.