Safety Critical Task Analysis (SCTA) is a well-established process in the UK onshore and offshore petrochemical and oil and gas sectors. It is a systematic process for the assessment and management of human failure.
What is particularly powerful about SCTA is the learnings that are gained. We generally aim to involve a mix of task experts in these sessions. Front line operators (with first-hand experience in carrying out the task) and process engineering and / or safety management roles (who can describe relevant process controls or process capabilities or who can comment about wider risk analysis). These individuals can provide different insights regarding process control.
For example, front line task experts can often clarify the correct method of task completion and/or describe problems associated with the task as currently performed (I.e. performance influencing factors), while process, safety or compliance experts can assist in judgements relating to the consequences of task failure, explain the purpose and function of current safeguards and/or comment on the viability of proposed additional safeguards.
Different people bring with them different opportunities to learn
This sharing of information often identifies gaps in the knowledge of the respective parties. For example, an operator may be unfamiliar with the purpose or function of a particular process safeguard and this knowledge gap is closed due to the input of the engineer or safety expert. Likewise, engineers/safety experts may have previously been unfamiliar with challenges associated with undertaking a task in a previously prescribed manner which is clarified by the operator. This knowledge exchange adds important substance to the task review process.
Frequently knowledge which is elicited during SCTA is not formally documented, rather it is tacit or held ‘in the heads’ of the experienced operators / engineers participating in the review. This may be knowledge which has developed over many years of plant experience (for example awareness of which valves do not fully close during an isolation, understanding of how a process column functions during an upset). Often, such insights are only formally shared when questions relating to process control are explored during the SCTA process. This presents the perfect opportunity to capture these insights with a view to closing gaps in knowledge and understanding.
A recent example – what operators understood versus what the risk assessment showed
During a recent SCTA examining road tanker offloading it was found that there was a valve on tanker offloading pipework which, due it is location, was difficult to access (it required climbing over pipework). The procedure for the task required this valve to be closed after a tanker transfer to site, however, over time (primarily due to accessibility) a practice had emerged whereby operators stopped closing this valve.
Questions were raised as to the requirement for this step (operators mentioned they didn’t routinely do it and saw no reason for it). However, the site safety engineer found a past safety assessment which stated that the valve was to be closed after tanker transfer as there was no backflow protection (NRV) on the line to protect against the entire tank contents flowing back down the transfer pipework to the loading point. Implementing a design modification was going to be complex, therefore the procedure step to close the valve had been added in the interim.
Clearly, in line with the hierarchy of control, engineered safeguards are required here. However, the SCTA process demonstrated a gap in awareness about the purpose of this interim measure. Had the risk analysis been done in isolation, with only either operators or only site engineers, it is unlikely this learning would have been achieved (until this point no-one knew operators weren’t closing the valve, and didn’t understand the reason for doing so). What is important is that the SCTA process identified this shortcoming, and improvements were made on the back of this. These sorts of learnings are commonplace during SCTA.
UK regulatory expectations
Competence management is a key Human Factors inspection topic on high hazard sites for the UK regulator, the Health and Safety Executive (HSE). Several success criteria are described in the HSE Human Factors COMAH delivery guide. However, a core expectation is that the competence management system is ‘clearly linked to local Major Accident Hazards’. Specifically, that competence standards are linked to safety critical procedures and take account of learnings from HF risk assessment activities such as SCTA.
Our approach to using the insights from SCTA to support the development of risk informed training and competence standards enables us to make this link.
Applying the process to develop risk informed competence standards
The following example demonstrates how we applied this process more formally to a LNG ship to shore transfer. The safety-critical task in question is the connection and preparation of a jetty unloading arm.
Step 1: The first stage of the process was to carry out a full HTA (Hierarchical Task Analysis) of the task. This provided a complete (step-by-step) representation of the task. The top level of this analysis is shown below.
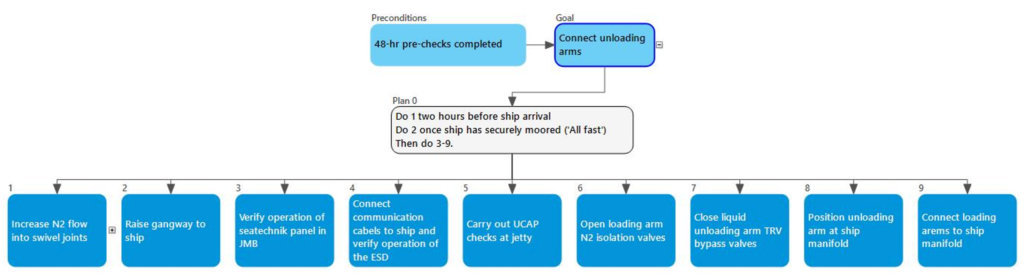
Step 2: The second stage was human failure analysis. This involved examining each step of the task analysis in closer detail, with a focus on the steps with potential MAH outcomes. The first subtask in the HTA was broken down to its discrete steps.
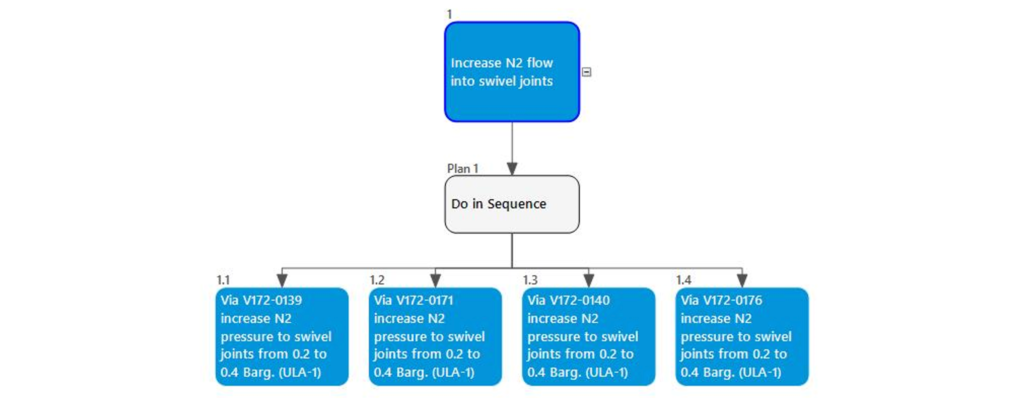
The sub-steps are identical in their detail, requiring the Operator to separately increase the flow of purge gas (Nitrogen) to each of the four jetty unloading arms. This raises the warm N2 flow across the swivel joints and removes any built-up moisture within. If this is not done, when LNG is subsequently introduced into the unloading arm, excess moisture at the joint could potentially freeze. The review team considered this to be potentially critical as any ice build-up at the swivel joint could restrict movement of the joint (which is meant to articulate freely to accommodate the movement of the ship in the tide) and potentially cause damage to the joint. The very worst-case outcome associated with freezing of the joint was considered to be serious damage of the unloading arm with potential loss of containment. This issue was therefore discussed in greater detail when carrying out the human failure/error analysis.
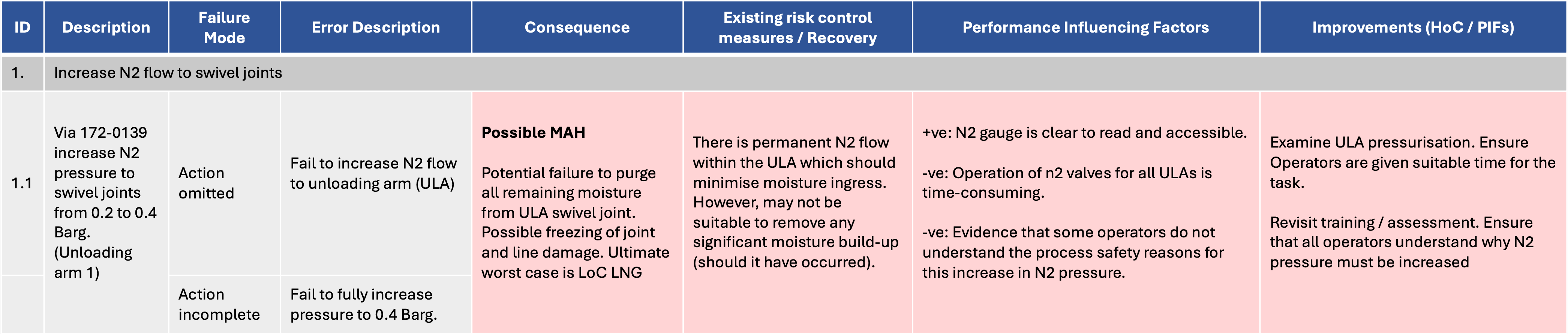
The SCTA identified an emerging issue associated with this task step. The team described several instances where LNG offloads had taken place where it was later found that N2 pressure had not been raised prior to the transfer because Operators responsible for these omissions had failed to appreciate the importance of this pressure increase. They recognised that there was already N2 flow across the swivel joints (existing 0.2 Barg N2 pressure) and, despite the procedure clearly indicating the requirement for an increase in pressure to 0.4 Barg, assumed that given the pressure rise was only minimal (0.2 Barg increase) that it was a ‘nice to have’ rather than an essential step in the task.
One contributory feature (an important performance influencing factor) was that it took additional time to increase the N2 pressure for each unloading arm as this involved opening N2 valves for each separate loading arm. Therefore, some operators had stopped performing this step.
The time-consuming series of steps and a lack of process understanding was contributing to the (frequent) omission of four safety-critical task steps. This prompted investigation into training. There was no individual competence standard for this task, rather operators received training in general principles associated with jetty operations. Competence assessment was managed by means of multiple-choice question sets and some high-level question and answer sessions with an assessor. The existing competence standard did require candidates to state what N2 pressure an unloading arm should be raised to prior to LNG offload. However, there was no clarification within training as to the importance of this step. Operators simply had to learn the answer to the question (i.e. the pressure should be raised to 0.4 Barg). Training and assessment weren’t focused on proving understanding where this was required.
It was explained that the reason for doubling N2 pressure from 0.2-0.4 Barg is that, even though this is a very small pressure rise, the pressure rise doubles the warm N2 flow over the swivel joint. It is this doubling of flow which is critical in the removal of excess moisture. Operators routinely ignoring this step had insufficient knowledge of the function of the process to appreciate why this was so important. This prompted us to develop a provisional task-specific competence standard for this procedure.
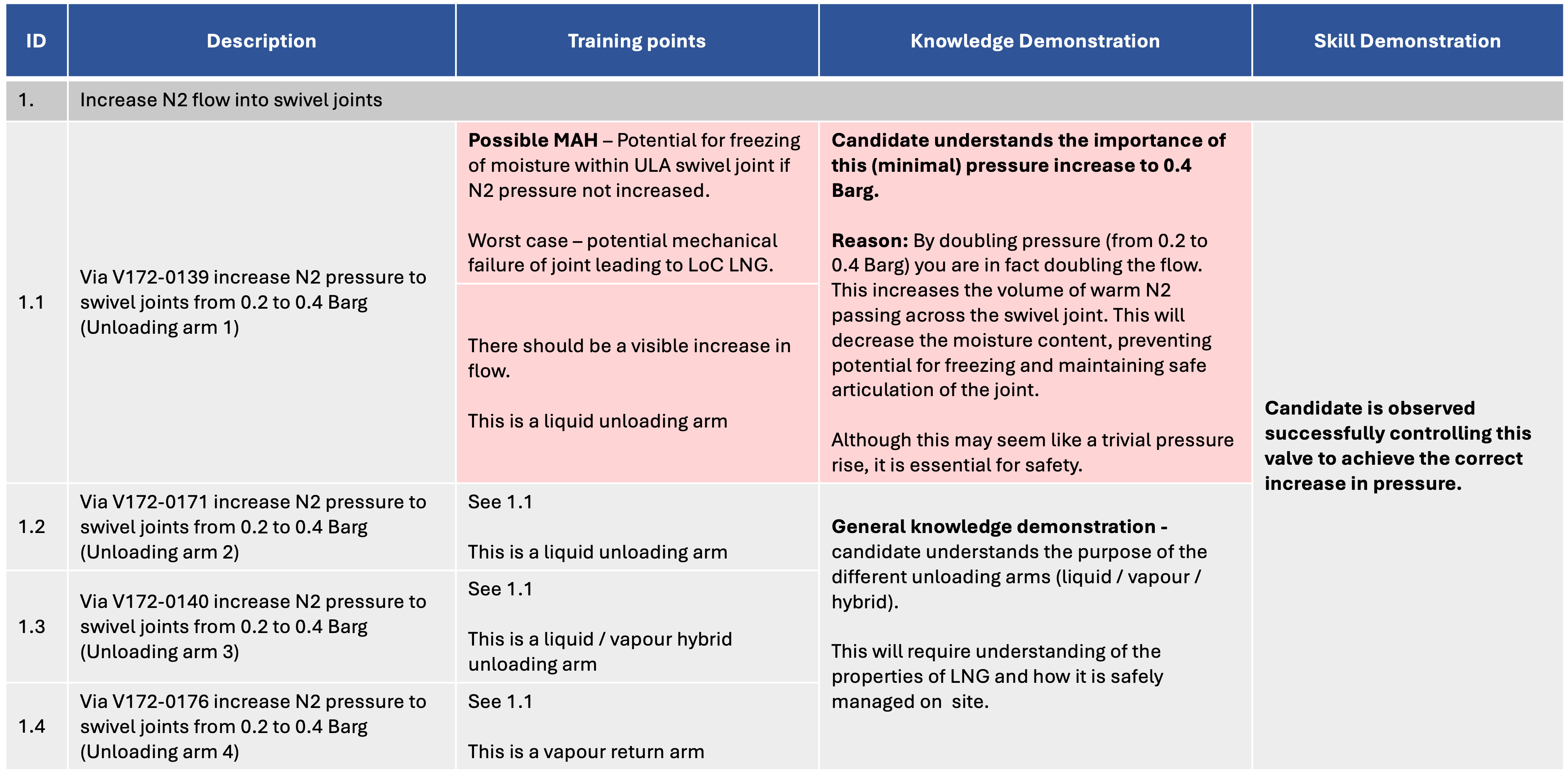
Step 3: The next stage is to record insights into competence. The structure of the document mirrors that of the task analysis. It also incorporated relevant risk analysis information which was gathered during human failure/error analysis. However, from a competence perspective this is where insights gained from SCTA can be recorded and used as the basis for the task-specific competence standard. It comprises two elements: Knowledge demonstration and Skill demonstration. This is based on the recognition that these are separate inputs into any MAH task-specific competence standard.
The Knowledge demonstration is an opportunity to record specific process, hazard and/or safeguarding knowledge and understanding that a candidate must demonstrate to prove their competence for this task. Ideally the standard should outline the specific knowledge demonstration and provide a clear description of the specific background knowledge which is required. This ensures that there is consistency to the training and assessment process – i.e. the same level of knowledge and understanding is verified for all prospective candidates regardless of which trainer performs the assessment. (Consistency of assessment can be a major issue if there are different assessors with varying knowledge, expectations and standards.)
The Skill demonstration provides an opportunity to record specific expectations which must be witnessed in relation to how a candidate physically performs the task. For example, the human failure/error analysis might indicate that it is important that a particular task step is performed correctly (e.g. carefully cracking open a valve at a high pressure-low pressure interface). This enables a record to be made within the competence standard to ensure that anyone being trained and assessed for this task is physically observed carrying out that step correctly. The skill demonstration helps to ensure that operators not only have the requisite knowledge necessary to undertake the task, but that their physical capability to carry out safety-critical task steps has also been verified. In the case of the above example, an important skill demonstration was that the candidate is physically observed controlling the valve to achieve the correct rate of N2 flow.
The focus here is on recording specific competence information which has not previously been, or is poorly, documented but has emerged during the SCTA process.
Conclusion
We have applied this method a several high hazard sites. Clearly this can generate a lot of data. However, the intention is that the information is used to develop risk informed competence standards (where they don’t already exist) or to augment existing training packages where there are gaps.
What is useful about the process is that it provides an extra dimension to the traditional SCTA approach. SCTA in itself is structured and systematic and provides for significant learning about hazards, vulnerability to error and the adequacy of existing safeguards (both engineering and administrative). When you have taken the time to assemble a group of task experts to facilitate SCTA, taking the process one step further to review training and competence is relatively simple. It makes excellent use of time and provides a further risk analysis output to support safety management.
We incorporate this process as part of our SHERPA software approach to Human Factors risk management.
If you are interested in this approach and would like to learn more about how we carry out SCTA and our thoughts on competence management, contact me at [email protected].
Alternatively visit our website at https://www.humanreliability.com for information on the other products and services HRA provide.