As of December 2023, the UK’s Health and Safety Executive (HSE) released the latest edition of the Human Factors (HF) Delivery Guide, featuring a revamped HF Roadmap detailed in Appendix 3. This guide aims to integrate human factors management into COMAH establishments, emphasizing the role of human factors risk assessment in reducing Major Accident Hazards (MAH) risks.
In this series, we will explore the various stages of the HF Roadmap and demonstrate how the Safety Critical Task Analysis (SCTA) process aligns with the roadmap to ensure a workplace that is not only safe but also efficient.
What is the Human Factors Roadmap?
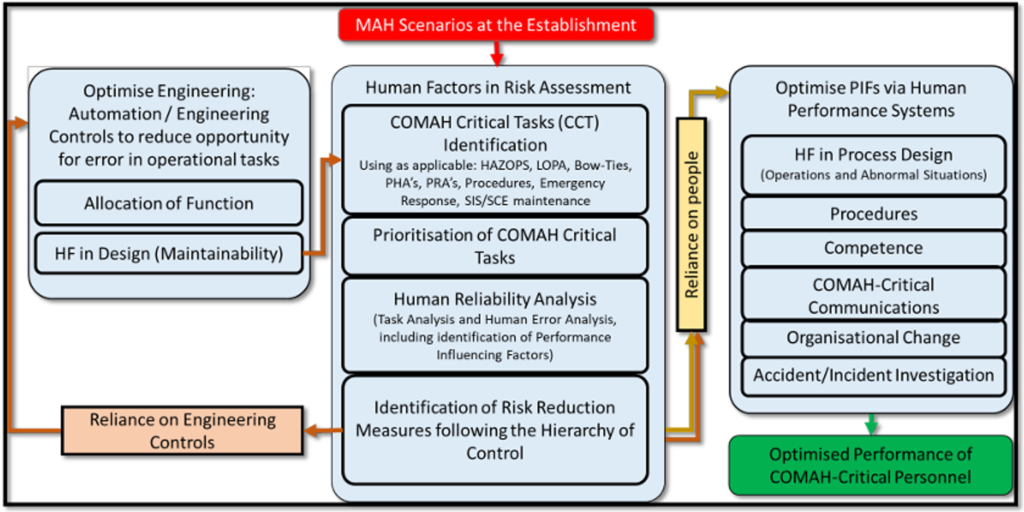
First published by the HSE in 2016, the HF Roadmap serves as a framework for integrating sustainable human factors management in COMAH establishments. It illustrates the impact of human factors risk assessment in reducing Major Accident Hazards (MAH) risks and highlights the importance of optimising any performance variables that could impinge work performance and challenges organisations to justify the current risk reduction measures in place. It follows the HSE’s Seven Steps Approach to managing human failures in MAH sites. These steps are:
- Step 1: Consider main study hazards
- Step 2: Identify manual activities that affect these hazards
- Step 3: Outline the key steps in these activities
- Step 4: Identify potential human failures in these steps
- Step 5: Identify factors that make these failures more likely
- Step 6: Manage the failures using Hierarchy of Control
- Step 7: Manage error recovery
In a way, the HF Roadmap illustrates how the steps above relate to each other. Due to this, the Roadmap plays a pivotal role in guiding COMAH sites in managing their safety-critical tasks, reducing the potential occurrence of MAH scenarios, and establishing efficient human performance.
What is Safety Critical Task Analysis (SCTA)?
Safety Critical Task Analysis (SCTA) is a technique used at HRA to help clients manage Human Factors at their site The beginnings of the technique can be traced back to SHERPA, which was first devised by our Managing Director, David Embrey. This influenced the approach used in the HSE Offshore Technology Report, OTO 1999/092 which laid the foundations for what we refer to as SCTA today. Other names for this approach include Human Factors Critical Task Analysis (HFCTR), Human Factors Critical Task Analysis (HFCTA) and SYSTEMS Critical Task Analysis (SCTA).
This first blog, Part 1, will delve into the various steps of the HF Roadmap with reference to the HSE’s Seven Steps Approach. In a later blog, Part 2, we will illustrate how we implement the roadmap in practice for an SCTA study by outlining a simplified and practical workflow.
Step 1: Considering the MAHs
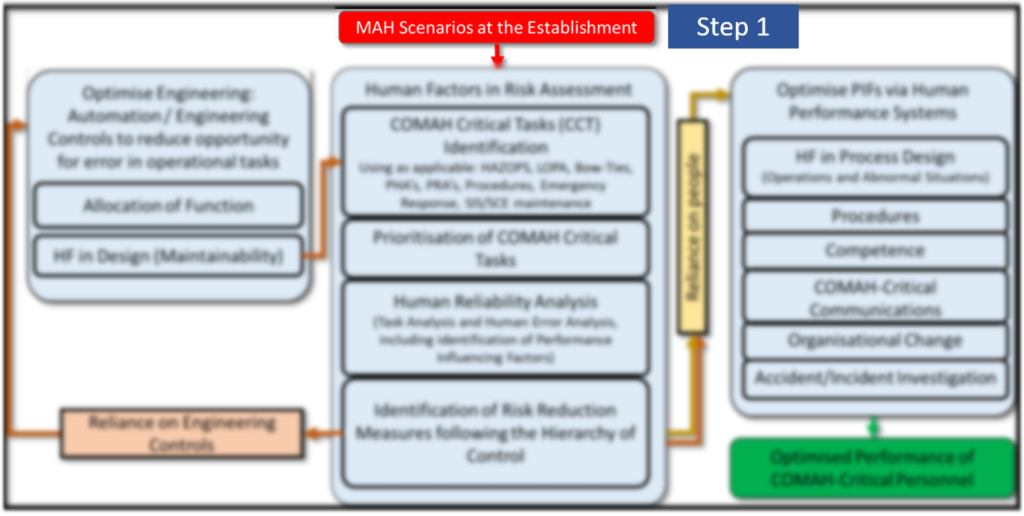
The first stage of the roadmap outlines that COMAH sites should identify their local MAH scenarios. The Control of Major Accident Hazards (COMAH) Regulations Guidance defined MAH as events arising from uncontrolled developments that could lead to serious danger to human health or to the environment and involve one or more dangerous substances as defined in the Control of Major Accident (COMAH) Regulations 2015.
Some resources that sites could use for identifying include previous safety reports or other risk assessment tools such as Hazards and Operability studies (HAZOP), Layers of Protection Analysis (LOPA), and Bow-Ties.
Step 2: Identifying and prioritising the critical tasks
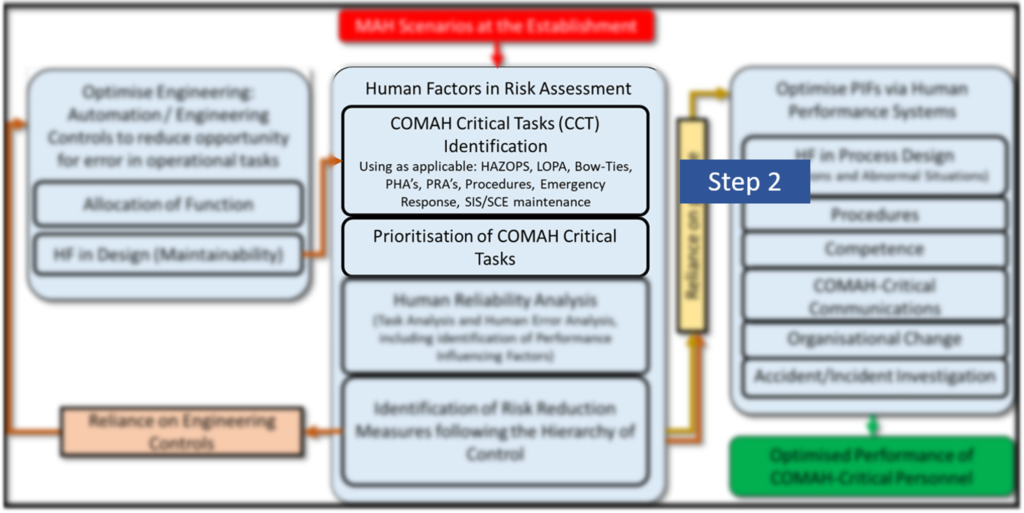
Once a site has identified the MAHs involved in their facility, they should then move towards compiling a list of the tasks relevant to these hazardous events, and to rank these critical tasks based on their risk. This is described as Step 2 in the HSE’s Seven Steps Approach “Identify manual activities that affect these hazards”.
This process typically involves references to HAZOP studies, LOPA, and other risk assessment tools in addition to inputs from process safety engineers, site personnel and subject matter experts. It is important for sites to focus on both routine and non-routine tasks in this initiative. This means that in addition to routine operational tasks, Maintenance, Inspection and Testing (MIT) tasks and emergency response tasks should be considered as well.
Once a list of safety-critical tasks has been completed, the tasks on this list should be prioritised to ensure that the site maximises its resource efficiency in managing human factors. When prioritising the tasks, key factors such as the severity of the consequences, the existing levels of engineering controls in mitigating the MAHs and the extent to which the task is reliant on people, should be taken into consideration. Insights from HAZOP studies, Bow-Tie Diagrams, and previous safety reports are also advantageous when ranking these tasks.
Step 3 – 5: Human Reliability Analysis
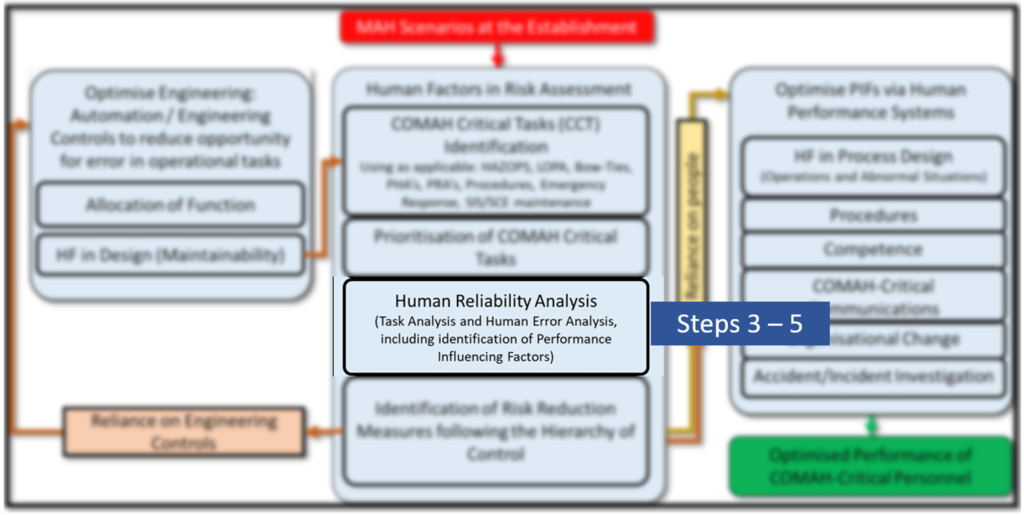
Now that the site has compiled its list of safety-critical tasks, they can move on to the next steps of the HF Roadmap, which is the Human Reliability Analysis. This analysis covers Steps 3 to 5 of the HSE’s Seven Steps approach, which are “Outline the key steps”, “Identify potentially human failures” and “Identify Factors that make these failures more likely”.
In the Human Reliability Analysis, the sites will select a task and analyse how the particular task is operated. This is known as Task Analysis, which is Step 3 of the HSE’s Seven Steps approach. The task analysis involves breaking the task down into individual steps to understand how the task is conducted and plays an important role as it provides plenty of opportunity for the site to ensure that any documentation of the task accurately reflects how it is done (Work-as-Imagined vs Work-as-Done). An example of a task analysis methodology would be the Hierarchical Task Analysis (HTA) as it ensures a complete representation of the task. Moreover, its graphical representation prompts the analyst to consider the potential human error at each level and component.
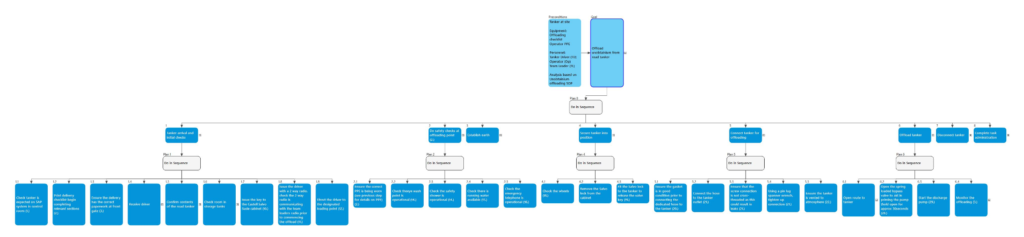
After the task analysis is completed, the analysis can proceed to identify the potential human errors that could occur (Failure Mode Analysis), which is Step 4. As the task analysis has been broken down into individual steps, it enables the analyst to consider the human error at each individual step, thereby providing a more thorough and complete analysis. Pairing the Failure Mode analysis is the Performance Influencing Factors (PIF) analysis which evaluates the factors that could affect the outcome of the task (Step 5). PIFs are any variables that could either positively or negatively affect the likelihood of a MAH. This includes generic PIFs, such as distractions and fatigue, as well as specific PIFs, like accessibility of the equipment or quality of the instructions.
Step 6: Managing the failures using hierarchy of control
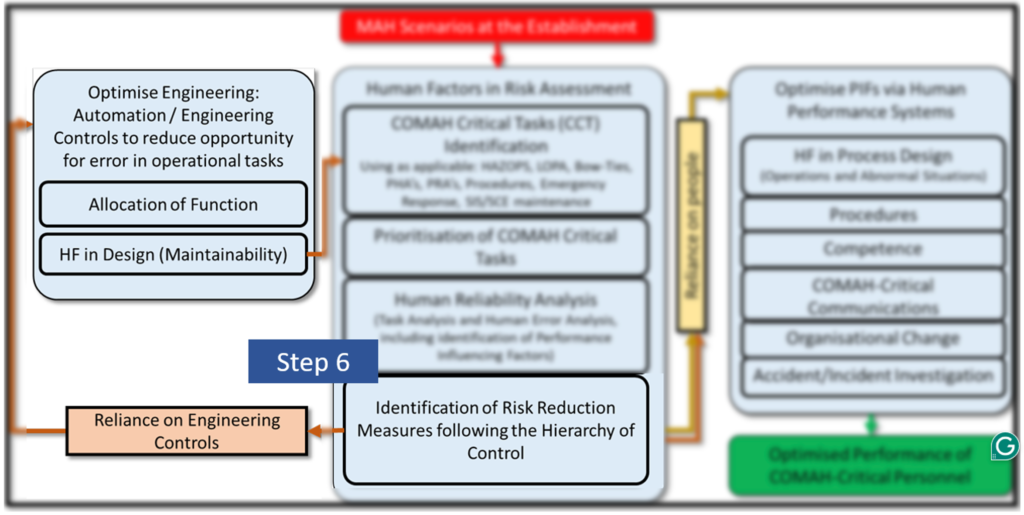
Step 6 involves an evaluation of the current Risk Control Measures (RCMs) present for the task and their effectiveness in preventing and/or mitigating the MAH outcome. This stage is quite critical as it forms the basis for understanding the extent to which the risks are managed. RCMs could range from engineering controls such as shut-off valves and trips to operator checks.
If the RCMs are heavily dependent on engineering controls, it is important that the sites review these controls in place to ensure that they are capable of preventing potential occurrences of MAHs. If these are proven to be inadequate, sites must take action to rectify this by considering improvements with reference to the Hierarchy of Control (HoC). In areas where there is reliance on the human element, it is important to ensure that they are justifiable for the task. For example, some checks are required by an operator in order to progress the task. If possible, the human element should be minimised as much as possible for safety purposes. However, if this is not practical, it is important to optimise the PIFs to hinder any human error.
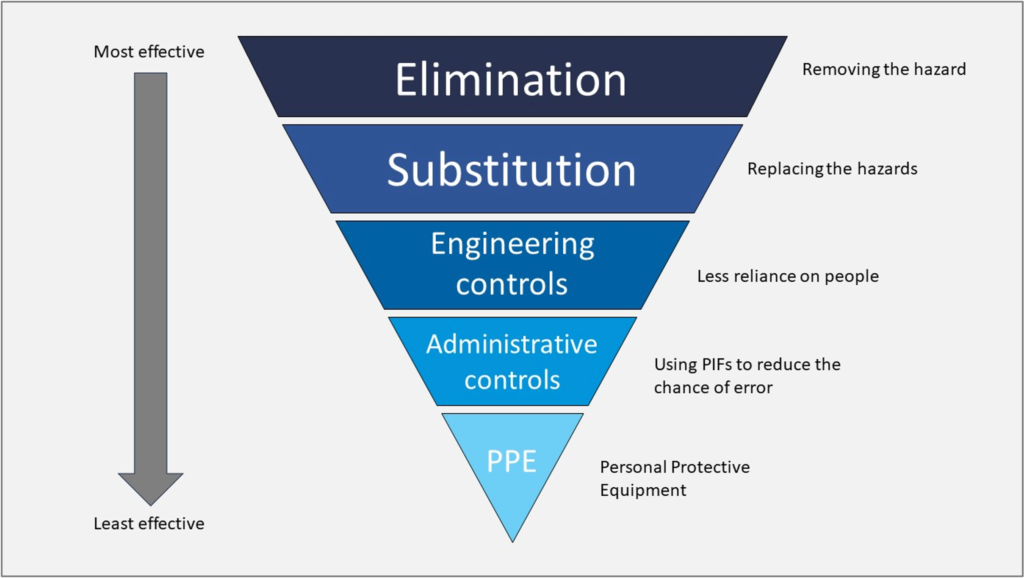
Step 7: Managing error recovery
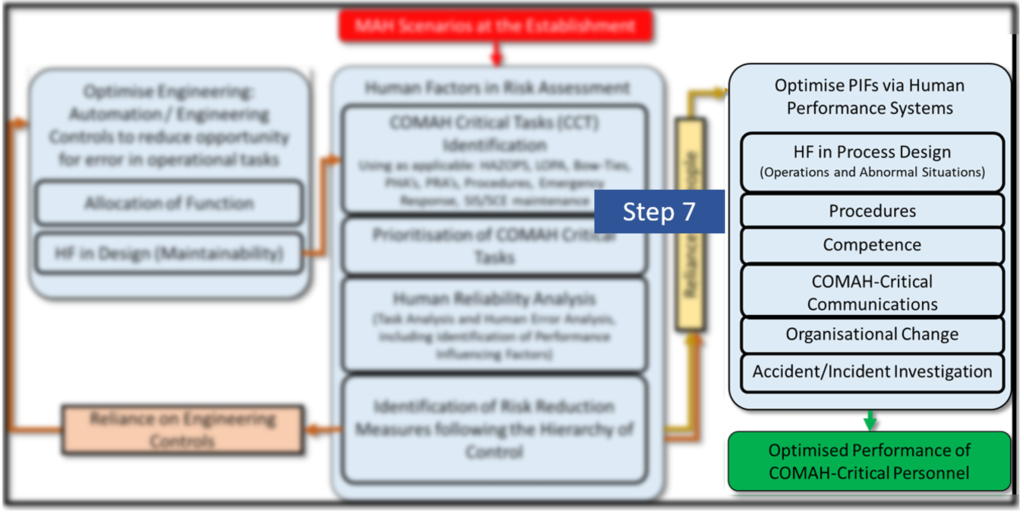
The final step of the Roadmap relates to Step 7 of the HSE’s Seven Steps Approach, “Managing error recovery”. It accentuates the importance of implementing improvements to mitigate human error and optimise performance. If the analysis has highlighted any gaps in the task, sites should progress towards addressing these gaps by reviewing the findings and implementing any necessary changes. This could be achieved by having good PIF management and optimising any PIFs found to have detrimental effects. For example, if the analysis highlighted some flaws with the procedure (e.g. the procedure is poorly written or has usability issues), then the site must consider improving its procedures by integrating some good practices for writing procedures. Some other ways to optimise PIFs include using job aids like checklists, introducing effective communication practices, and managing organisational changes.
Conclusion
To summarise, the HSE’s HF Roadmap was published as a framework for COMAH sites in managing human performance. In this blog, we provide a brief overview of each steps of the HF Roadmap. In Part 2, we will provide the SCTA workflow to exemplify implementing the HF Roadmap in practice.
Whether you’re looking to enhance your grasp of the HF Roadmap or embark on the journey of conducting SCTAs, our courses are crafted to cater to your specific learning needs.
If you’re eager to deepen your understanding of the HF Roadmap and the HF Delivery Guide, our HF_PLC coursepresents an excellent opportunity. This course is tailored to provide comprehensive insights into the intricacies of human factors management within COMAH establishments.
On the other hand, if you’re keen on mastering the art of conducting Safety Critical Task Analyses (SCTAs), our flagship SCTA course offers a robust foundation, equipping you with the skills and knowledge necessary to navigate the complexities of SCTAs effectively.