1. Introduction
Performance Influencing Factors (PIFs) play a crucial role in understanding and managing human reliability in safety-critical industries. While many practitioners are familiar with the Health and Safety Executive’s (HSE) PIF list, which provides a solid foundation for human factors analysis, there’s much more to consider when we look deeper into how various factors influence human performance.
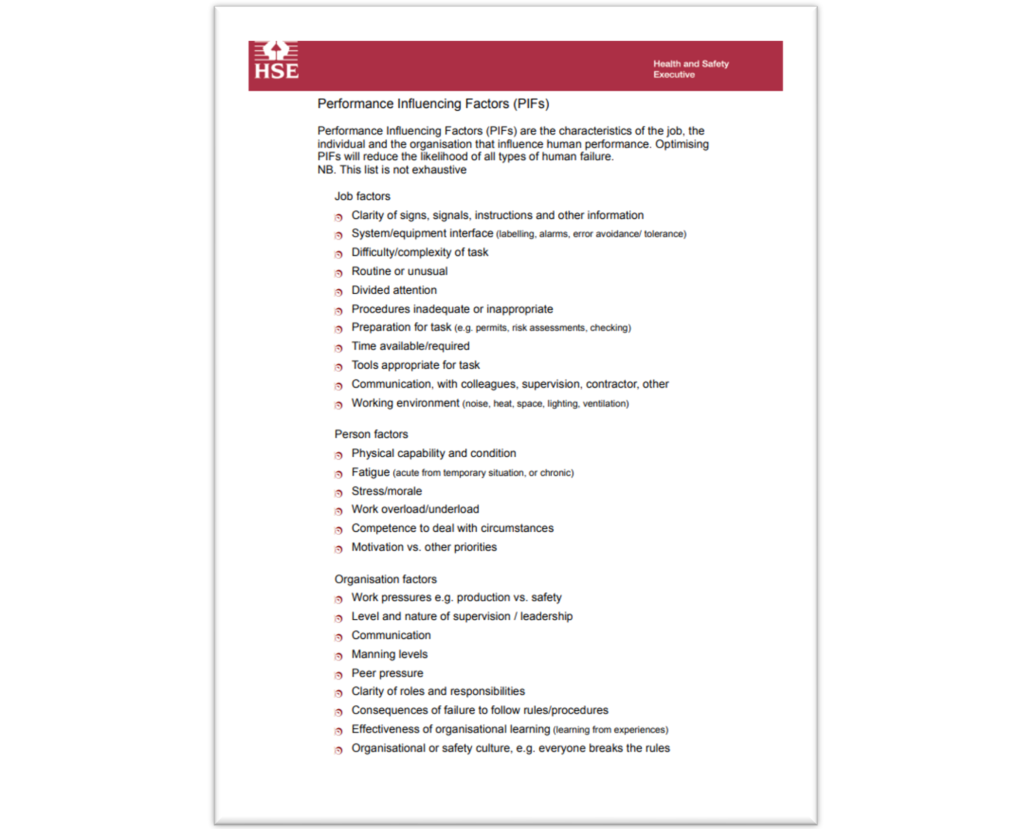
In my experience working with different organisations, I’ve found that relying solely on standard PIF lists can lead us to miss important influences on human performance. These lists serve as excellent starting points, but they can inadvertently create a ‘checkbox mentality’ where we focus only on obvious, immediate factors while missing subtle yet powerful influences on performance.
This blog post aims to expand our perspective beyond the basic categorisation of PIFs. We’ll explore different types and scales of influence, examine how some PIFs are static while others are dynamic, and delve into the crucial but often overlooked realm of latent PIFs that create the conditions for future incidents.
2. The Traditional View
The HSE’s approach to PIFs provides a structured framework that categorises influences into three main areas: Job, Person, and Organisation factors. This categorisation has served the industry well as an initial approach to understanding performance influences. The diagram below is taken from HSG48: Reducing error and influencing behaviour.
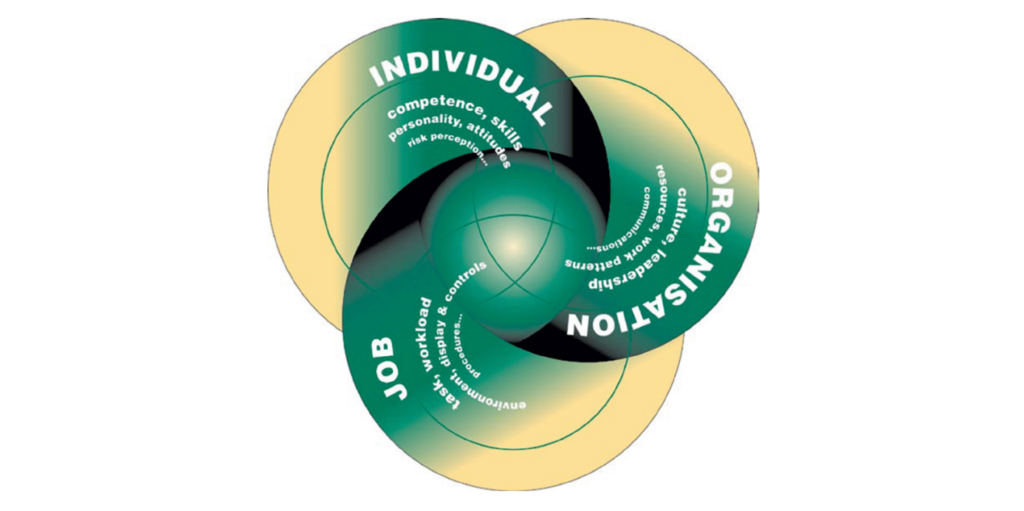
Job factors typically include elements like the clarity of signs and signals, system interfaces, task complexity, and the working environment. Person factors encompass individual characteristics such as physical capability, fatigue, stress, and competence. Organisational factors cover aspects like work pressures, supervision, communication, and safety culture.
While this categorisation is useful, it has limitations. First, it tends to focus on immediate, observable factors rather than deeper systemic influences. Second, the categories can create artificial boundaries – in reality, many PIFs span multiple categories or interact in complex ways. For instance, is poor communication during shift handover a job factor, a person factor, or an organisational factor? The answer is often “all of the above.”
Additionally, the traditional view might lead us to treat PIFs as static elements that can be checked off a list, when in reality, many are dynamic and context dependent. The same factor might have different levels of influence depending on the specific situation, time of day, or combination with other factors.
As we move beyond this traditional view, we need to consider not just what factors are present, but how they interact, how they change over time, and how they influence different types of performance outcomes.
3. Different Scales of PIFs
When we move beyond traditional categorisations, we can identify PIFs operating at different scales of influence. Understanding these different scales helps us conduct more thorough and effective analyses of performance influences.
3.1 Generic PIFs
Generic PIFs are those factors that influence performance across many different tasks and situations. These are often the “usual suspects” that appear in standard checklists, but their influence can be profound and far-reaching. Examples include:
- Environmental conditions (lighting, noise, temperature)
- Basic competency requirements and training
- Standard communication protocols
- General workplace layout and accessibility
- Basic equipment maintenance standards
While these factors might seem obvious, their generic nature doesn’t make them any less important. In fact, their broad influence means that any deficiencies can have wide-ranging impacts across multiple tasks and activities.
3.2 Task-specific PIFs
Task-specific PIFs are unique to particular activities and might not appear on standard checklists. These become apparent only when we analyse specific tasks in detail. Examples include:
- The positioning of specific valves or controls for a particular operation
- Specialised tool requirements for maintenance tasks
- Task-specific communication needs (like three-way communication for critical operations)
- Specific environmental challenges (like working at height or in confined spaces)
- Unique time pressures associated with particular processes.
Understanding task-specific PIFs requires detailed task analysis and often reveals influences that might be missed in more general assessments.
3.3 Failure Mode Specific PIFs
Different types of human error are influenced by different factors. Understanding how PIFs relate to specific error types helps us target our interventions more effectively:
For Slips (actions not carried out as intended):
- Equipment and control layout
- Interface design clarity
- Similar-looking equipment or controls
- Lighting and visibility
- Physical access and ergonomics
- Time pressure effects on accuracy
- Interruptions during physical tasks
For Lapses (memory failures and omissions):
- Procedure and checklist design and usability
- Task interruptions and distractions
- Task complexity and number of steps
- Workload and attention demands
- Shift handover quality
- Availability of memory aids
- Prominence of task progress indicators
For Mistakes (knowledge or rule-based errors):
- Training adequacy for specific scenarios
- Availability and quality of procedures
- Clarity of rules and guidelines
- Experience with similar situations
- Complexity of decision-making required
- Quality of mental models
- Availability of technical support
- Time for problem-solving
For Non-compliance (deliberate deviation):
- Perceived production pressure
- Procedure practicality and usability
- Equipment availability and condition
- Organisational safety culture
- Previous experience of “successful” violations
- Peer and supervisor attitudes
- Effort required for compliance
- Visibility and enforcement of rules
- Understanding of risk and consequences
By considering PIFs in relation to these specific error types, we can better target our interventions and controls. For instance, if we’re concerned about slips, we might focus on physical design and layout factors. If non-compliance is the issue, we need to look more closely at organisational and cultural factors that might be driving deliberate deviations.
Static vs Dynamic PIFs
Understanding the temporal nature of Performance Influencing Factors adds another crucial dimension to our analysis. Some PIFs remain relatively constant over time, while others fluctuate – sometimes predictably, sometimes not. This distinction is vital for how we assess and manage these factors.
4.1 Static PIFs
Static PIFs are relatively stable conditions that don’t change significantly without deliberate intervention. These include:
- Physical layout of equipment
- Permanent labelling and signage
- Design of interfaces and controls
- Basic procedural requirements
- Standard operating protocols
- Structural aspects of the organisation
While these factors are static, we shouldn’t take them for granted. Regular assessment is still necessary to ensure they haven’t degraded over time or been compromised by modifications or workarounds.
4.2 Dynamic PIFs
Dynamic PIFs change over different timescales and can significantly impact performance. Understanding these variations helps us anticipate and manage their effects:
Short-term variations (hours/days):
- Individual alertness levels through a shift
- Weather conditions affecting outdoor work
- Staffing levels due to illness or absence
- Equipment availability
- Production demands and time pressure
Medium-term variations (weeks/months):
- Seasonal changes affecting working conditions
- Maintenance schedules impacting equipment reliability
- Staff experience levels as people rotate roles
- Changes in production targets or priorities
- Project deadlines and associated pressures
Long-term variations (months/years):
- Workforce competency as experience builds or staff turnover occurs
- Equipment condition and reliability
- Organisational culture evolution
- Changes in management priorities
- Market pressures and their impact on operations
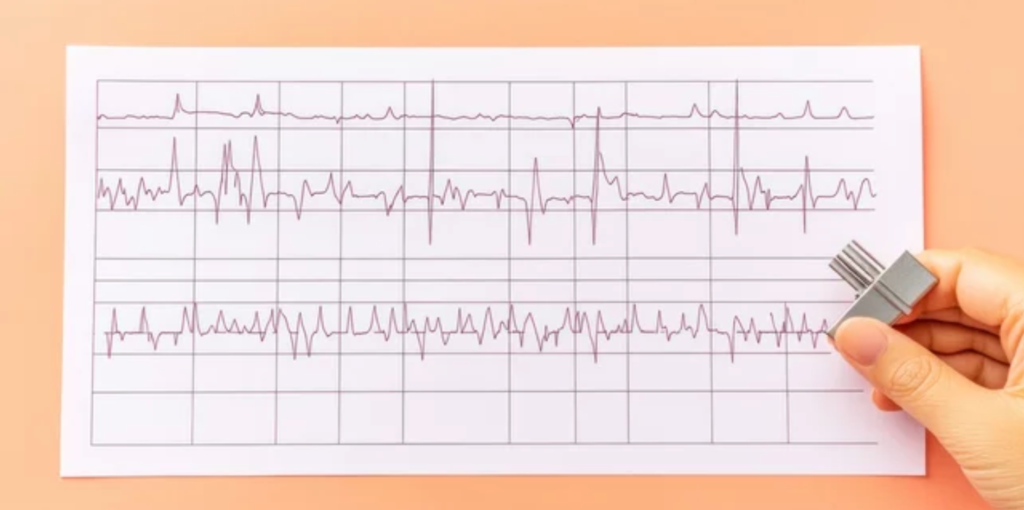
4.3 Managing Dynamic PIFs
The dynamic nature of these factors requires different management approaches:
- Regular monitoring and assessment
- Flexible response strategies
- Forward planning for predictable variations
- Building resilience into systems and procedures
- Training staff to recognise and adapt to changing conditions
Understanding the static or dynamic nature of PIFs helps us develop more effective assessment and management strategies. Static factors might need less frequent but more thorough assessment, while dynamic factors require ongoing monitoring and adaptive management approaches.
5. Latent PIFs
While immediate PIFs affect task execution, latent PIFs influence organisational decisions and conditions that can create the foundation for future incidents. These factors often operate subtly over time, influencing critical decisions and creating vulnerabilities in the system.
5.1 Design-Related PIFs
Latent PIFs can significantly impact design decisions and modifications through various interrelated factors. Budget constraints often force compromised design choices, while time pressure during design phases can lead to rushed decisions. The design process can be further compromised by limited user input, inadequate review processes, poor communication between design and operations teams, and a lack of specific design expertise in critical areas. These factors don’t operate in isolation but often combine and interact to influence design outcomes.
These design-related latent PIFs can manifest in various types of performance failures. Poor equipment accessibility might result in incomplete maintenance actions, while inadequate information displays can lead to wrong operational decisions. Systems might suffer from delayed responses due to poorly designed alarm systems, and unintuitive system layouts can result in operators omitting crucial actions entirely. These consequences often remain hidden until specific circumstances arise that expose the underlying design weaknesses, making them particularly challenging to identify and address proactively.
It is important to incorporate good quality Human Factors advice and work within the design process.
5.2 Management Decision PIFs
Management decisions about safety and operations are shaped by a complex web of organisational factors. Production targets and commercial pressures often create competing priorities, while resource constraints across financial, personnel, and time dimensions can limit available options. The quality of decision-making is further influenced by incomplete or delayed feedback from operations, organisational structure and reporting lines, performance measurement systems, risk perception, and the organisation’s previous experience with incidents. These factors create the context within which management must make critical safety decisions.
The impact of these management-level PIFs often manifests in patterns of delayed or inadequate safety responses. Safety improvements may be postponed, recommendations might be only partially implemented, and safety measures could be incorrectly prioritised against other business objectives. Perhaps most critically, there can be a tendency toward premature closure of incident investigations, potentially missing deeper systemic issues. These outcomes typically emerge gradually, making it challenging to connect them directly to the management-level factors that influenced them, yet their impact on system safety can be profound.
5.3 Organisational Learning PIFs
An organisation’s capacity to learn and adapt is influenced by several interconnected systemic factors. The foundation begins with the quality of incident reporting systems and the effectiveness of communication channels that allow information to flow throughout the organisation. This learning capability is further shaped by the time allocated for learning activities, the status and influence of safety personnel within the organisation, and the cultural willingness to acknowledge problems openly. The effectiveness of the learning process is also determined by the quality of performance indicators that guide improvement efforts, and the pressure exerted by external regulatory bodies that can drive organisational change.
These organisational learning factors directly influence various types of failures within the system. Poor organisational learning often results in critical actions being omitted from procedures, as lessons from past experiences fail to be incorporated into standard practices. Decision-making quality suffers when there is incomplete understanding of past events, while inadequate feedback systems lead to delayed improvements in processes and procedures. Perhaps most concerning is when corrective actions remain incomplete due to inadequate follow-up, creating a cycle where the same issues may recur because learning opportunities weren’t fully captured and implemented.
5.4 Cultural and Systemic PIFs
Cultural and systemic PIFs operate at the deepest level of organisational influence, creating the fundamental context within which all other factors operate. The power distance within an organisation shapes how information flows and decisions are made, while approaches to blame and accountability influence reporting and learning behaviours. These cultural elements are often deeply rooted in historical decisions and their ongoing legacy, as well as broader industry norms and practices. The organisation’s identity, values, and leadership styles create an overarching framework that determines how safety is prioritised and managed relative to other organisational goals.
The influence of these deep cultural factors manifests in various forms of performance deviation. Cultural pressures can lead to poorly timed decisions, with actions taken either too early or too late based on organisational dynamics rather than operational needs. The normalisation of deviance can result in incomplete actions becoming accepted practice, while groupthink might lead to wrong decisions going unchallenged. Perhaps most significantly, cultural barriers to speaking up can result in critical actions being omitted entirely, as workers may feel unable to voice concerns or challenge existing practices. These cultural influences are often the most difficult to identify and address, yet they can have the most pervasive impact on system safety.
Understanding these latent PIFs helps explain why organisations sometimes fail to:
- Implement recommendations fully
- Learn effectively from incidents
- Maintain safety standards over time
- Make timely decisions about safety
- Allocate resources appropriately
By identifying and managing these latent PIFs, organisations can better address the root causes that create conditions for future incidents, rather than just dealing with immediate performance factors.
6. Practical Implications and Best Practices
6.1 Recording PIFs
Effectively, when documenting PIFs, the quality and specificity of documentation can significantly impact their usefulness. Here are key principles for recording PIFs:
Include Directional Indicators
- Always specify whether a PIF is positive (+ve) or negative (-ve)
- Examples: “-ve LAYOUT: Valves are positioned above head height requiring ladder access.”
Provide Specific Context Instead of vague labels, include detailed explanations:
Poor Documentation:
- “-ve DISTRACTION”
- “-ve WORKLOAD”
- “+ve SUPERVISION”
Effective Documentation:
- “-ve DISTRACTION: Task conducted in high-traffic area near shift changeover point.”
- “-ve WORKLOAD: Single operator managing three concurrent batch processes.”
- “+ve SUPERVISION: Dedicated supervisor present during critical valve alignments”
Link to Specific Failures or Tasks Connect PIFs to specific concerns:
- “-ve HMI: Digital display updates too slowly to detect rapid pressure changes.”
- “+ve PROCEDURE: Step-by-step photos provided for complex assembly sequence.”
- “-ve ACCESS: Gauge reading requires awkward body positioning in confined space.”
6.2 Practical Tips for PIF Analysis
- Systematic Approach
While standard PIF checklists provide a useful starting point, effective analysis requires looking beyond these basic frameworks. Consider how factors influence performance at different scales, from generic organisational influences through to task-specific challenges. Pay particular attention to both static conditions that remain relatively constant and dynamic factors that change over time. Always investigate latent conditions that might create the foundations for future incidents.
- Data Collection Methods
Effective PIF analysis draws on multiple sources of information. Direct observation of tasks in their actual context provides crucial insights that might be missed in documentation alone. Structured interviews with operators can reveal subtle influences and informal practices. Historical data from incident reports and near-miss records often highlights recurring issues. Reviewing procedural documents helps identify potential gaps between work-as-imagined and work-as-done.
- Common Pitfalls to Avoid
Many organizations fall into the trap of treating PIF analysis as a checkbox exercise, relying too heavily on generic lists. Remember to consider positive factors that enhance reliability, not just negative influences that might degrade performance. Look beyond immediate task conditions to understand latent organisational and cultural factors. Pay attention to how factors might vary across different times, situations, and conditions. Finally, ensure findings are documented with sufficient detail and context to support effective action – vague labels without explanation limit the value of the analysis.
7. Conclusion
Moving beyond basic PIF lists requires a more nuanced and comprehensive approach to human performance analysis. By understanding different types of PIFs, their various scales of influence, and particularly their latent effects, we can better identify and manage factors that influence human performance.
Key takeaways:
- PIFs operate at multiple levels from immediate task influences to latent organisational conditions.
- Different error types are influenced by different combinations of PIFs.
- Documentation quality is crucial for effective PIF analysis.
- Consider both static and dynamic factors.
- Look beyond obvious immediate factors to identify latent conditions.
The future of PIF analysis lies not in longer checklists, but in better understanding of how various factors interact and influence performance across different timeframes and organisational levels. By taking a more sophisticated approach to identifying and documenting PIFs, we can better support human performance and system safety.
PIF improvements should complement Hierarchy of Control (HoC) improvements, but we’ll leave that discussion for a future blog.
8. Acknowledgment:
Thanks to my colleagues at HRA who have contributed to these ideas through many discussions, e.g. David on distinguishing between static and dynamic PIFs, Richard and Jamie on recording PIFs, Neil on feedback to the blog, and many other discussions.
This article was developed through an extensive collaboration with Claude 3.5 Sonnet, an AI assistant created by Anthropic. The process involved multiple iterations of drafting, review, and refinement to structure the content and articulate complex concepts clearly. While I guided the direction and drew upon my expertise in human factors, Claude helped shape the article’s organisation and contributed to crafting clear, accessible explanations of technical concepts. This partnership demonstrates how AI tools can support technical writing while maintaining the author’s voice and domain expertise.
Further reading
Visit our webpage on Performance Influencing Factors (PIFs).
We’ve also written a previous blog on Positive PIFs.
Come on our flagship SCTA course!
If you’ve enjoyed this article and want to have more opportunity to learn then come on our flagship course on Human Factors Safety Critical Task Analysis (SCTA). Find out more here: https://the.humanreliabilityacademy.com/courses/human-factors-SCTA