Human Factors and Quality Improvement are friends.
I’ve spent the last 15 years immersed in the realm of human factors. From academia to practical applications in various sectors like healthcare, oil, gas, and chemical industries, my journey has been driven by a passion for optimizing human performance within complex systems – making safe work easier to do.
Over that time, I’ve experienced lots of organisations in different sectors at different states of Human Factors maturity:
- Unaware: Little measure, acknowledgment or feedback of problems related to human performance issues. Other organisational issues draw attention and individuals are likely blamed as bad apples in an otherwise functioning system. There is not a good grasp of what is going on or the extent of the problem. [A ‘what’ problem];
- Symptom aware: Realisation there is a recurring systematic issue with human performance, perhaps through near misses, incidents, and issues of non-compliance but no one knows why. [A ‘why’ problem];
- Problem aware: Realisation there is a human performance issue which has had little attention that can be addressed through the discipline of Human Factors, however they don’t know how. The big shift here is that individuals are not the root cause of the performance problems, instead it is more to do with the way the system is designed, organised and managed that influences system performance. [A ‘how’ problem];
- Solution aware: Understanding an approach or methodologies that can be applied to resolve or mitigate some of these performance issues through listening and learning from staff, and taking a people centred design approach to the system.
Moving towards Level 4, in this article we delve into a methodology that’s been instrumental in our work: SYSTEMS Critical Task Analysis (SCTA). This offers a distinct approach tailored to dissecting critical tasks within high-stakes environments. Systems Critical Task Analysis focuses on critical risks, applies Human Factors knowledge and techniques, engages staff to learn about work-as-done, provides practical and actionable improvements to reduce risks associated with error and makes safe work easier to do.
We present a case study focusing on a critical task in the pharmaceutical manufacturing sector. This organisation in which the study was conducted was around Level 2 and 3 and so more receptive to hear about solutions.
Unveiling the Methodology: A Quick Overview
SCTA encompasses three core elements:
- Task Analysis: A meticulous examination of the task at hand.
- Failure Analysis: Identifying potential human failures within the task.
- Performance Influencing Factors (PIFs) Analysis: Assessing factors that influence task performance, either mitigating or exacerbating the likelihood of failure.
This structured approach allows us to navigate through the complexities of critical tasks, pinpoint vulnerabilities, and devise targeted interventions.
In the case study that follows we also highlight two other important elements of the SCTA process, which enhance Human Factors Risk Management:
- Principle risk identification: A discussion to highlight what the key hazards are related to the task, essentially: why are we looking at this task?
- Risk screening: Mapping out what steps are related to the key hazards, have a high human involvement and are vulnerable to failure.
The Case Study: Autoclave Preparation in Pharmaceutical Manufacturing
Autoclaves are used for sterilizing equipment. You load the equipment into an autoclave chamber which subjects the equipment to high pressure steam at high temperature, which kills off pathogens and bacteria. The equipment is then fit for use in a sterile environment.
Preparing for the autoclave in our task involved the preparation of a trolley full of equipment to be used in the sterile environment on the other side of the autoclave chamber. The different equipment needed to be identified, put in bags according to the instruction, and placed on the trolley in a certain way.
Preparing a trolley for autoclave sterilisation isn’t just a routine task but a meticulously orchestrated process crucial for ensuring product quality, safety, and compliance.
Principle risk identification
In the case study we were lucky enough to speak to pairs of workers from different shifts. One of the first things we asked them was what they were worried about in relation to the task, what could go wrong, what could lead to a really bad outcome.
There wasn’t a consistent message from the different people that we spoke to, other than the potential for equipment to still be wet after the autoclave which they didn’t seem to have much control over. This would mean that they would need to be sterilised again.
Staff would also raise issues, and raise even more issues when things came to mind, similar to a brainstorming exercise.
Ideally, reflecting on best practices in other industries we work in, although not everyone achieves these high standards, staff would be risk informed, the principle risks would headline their training and their procedures. When asked about the principle risks staff should ideally be able to rattle off the top 3-5 risks that are related to that task.
Collectively, with the staff, and through the analysis we created a table of principle risks. Gaining clarity about the principles risk related to a task is important for risk management.
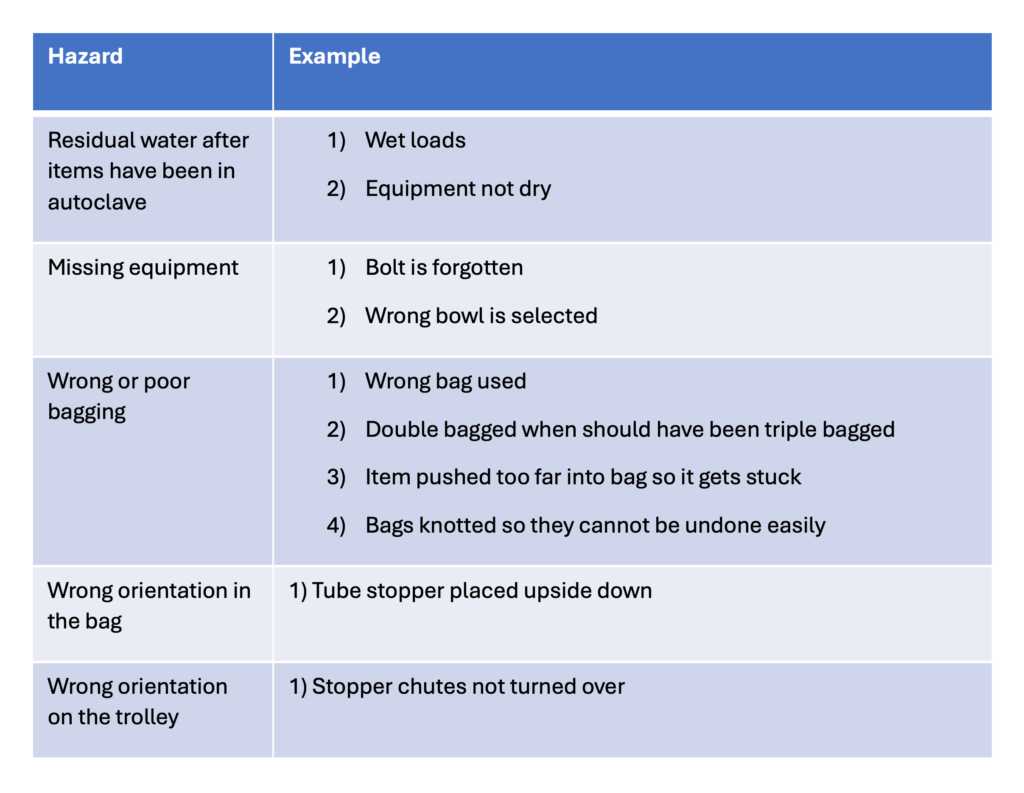
Task Analysis: Bridging work-as-imagined and work-as-done
We started the Hierarchical task Analysis (HTA) by working from the procedure (work-as-imagined). We then engaged with operators, checking and dissecting each step of the process (work-as-done). We generally find there is always a gap between work-as-imagined and work-as-done, it is more a question of how big the gaps are, and whether they are meaningful.
Autoclave preparation was a very repetitive task, doing almost the same thing with different bits of equipment. However, each piece of equipment was different and sometimes they had special instructions, e.g. a few items needed to be triple bagged rather than double bagged. This sort of repetitive task with similar but different tasks steps could be prone to error.
The image below shows a small branch of the HTA for preparing the stopper tubes for the autoclave:
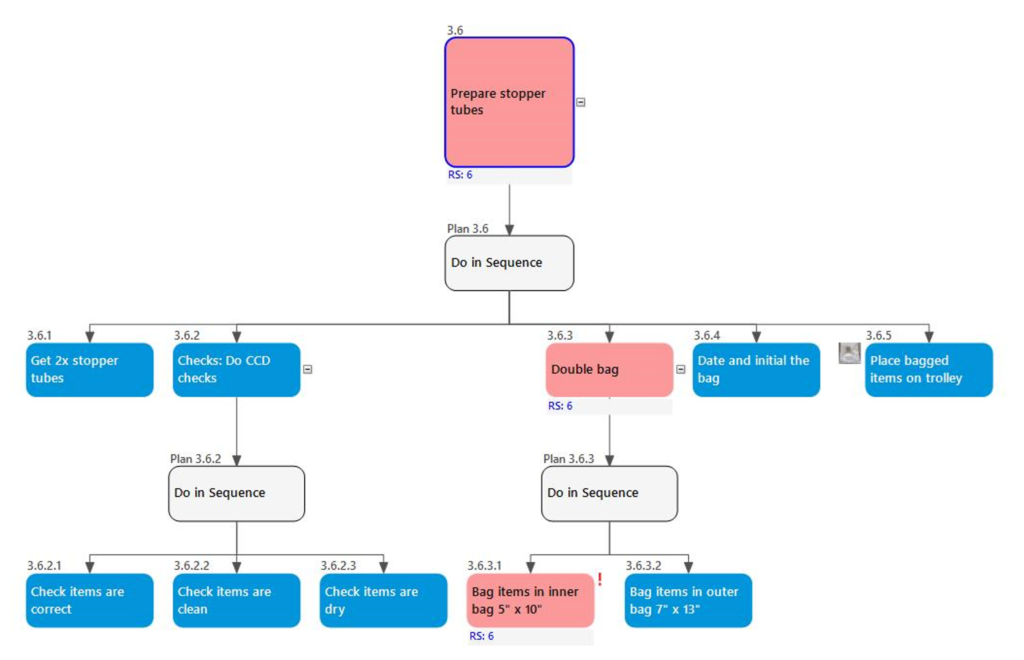
Risk Screening: Where are the hot spots?
Once the task analysis was completed we wanted to move on to the risk assessment. However, to use our time most efficiently we first of all wanted to identify where the main risks were, so we could pay more attention to those steps and less where staff were less concerned.
We moved through the task analysis highlighting steps and branches in red (related to key risk and vulnerable to failure), amber (related to key risk but less vulnerable to failure), and green (of less concern from a risk management perspective).
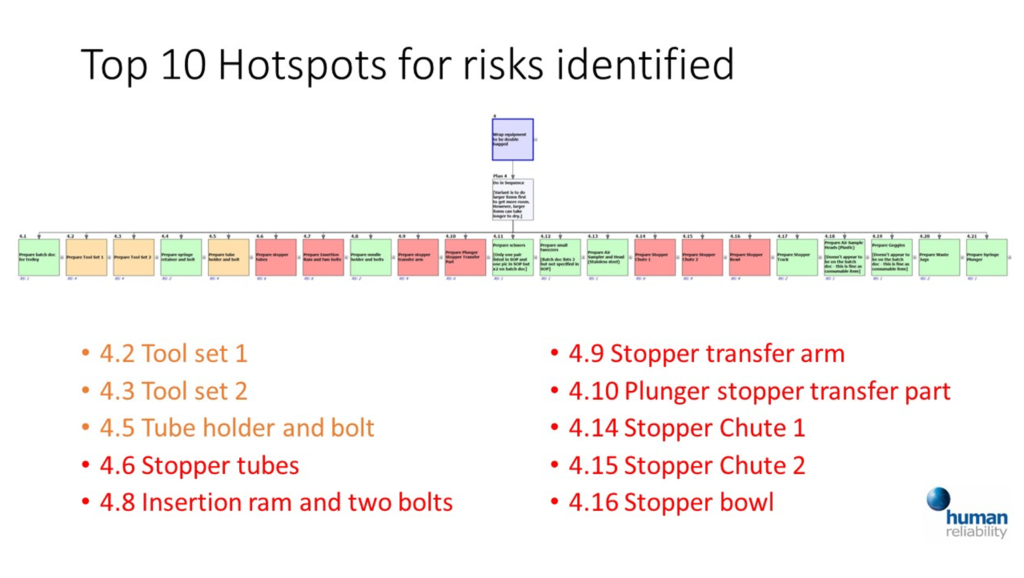
Failure and PIF Analysis
Following the SCTA methodology we were then able to have a structured conversation about the potential failures related to the different steps, how they could go wrong, why, and what factors made errors more likely or less likely – Performance Influencing Factors (PIFs).
Example issues:
- Out of 20 items, 3 needed to be triple bagged rather than double bagged. This detail could be overlooked and infrequently people would double bag some of these items. Some improvement to consider were:
- Improve readability of triple bagging so less likely to miss
- In addition add a warning to SOP
- Consider grouping all triple bagging items together so they are done at the same time
- The stopper transfer arm has to be assembled correctly, there is a right way and a wrong way. It is easy to place on the wrong way and hard to check. Ideally we would design the equipment so it can only be placed on the correct way. If that cannot be done then we would want to make it more obvious which is the right way and which is the wrong way.
- Sometimes people preparing the trolley tie the bags closed too tightly. This causes problems for the people on the sterile side who struggle to undo them. One issue here was the acknowledgement that training was inconsistent.
- The stopper tubes needed to be placed in the bag a certain way, but people sometimes put them in upside down. One of the major factors here was that the supporting picture in the procedure was actually upside down, which is a bit of an error trap that could be easily rectified.
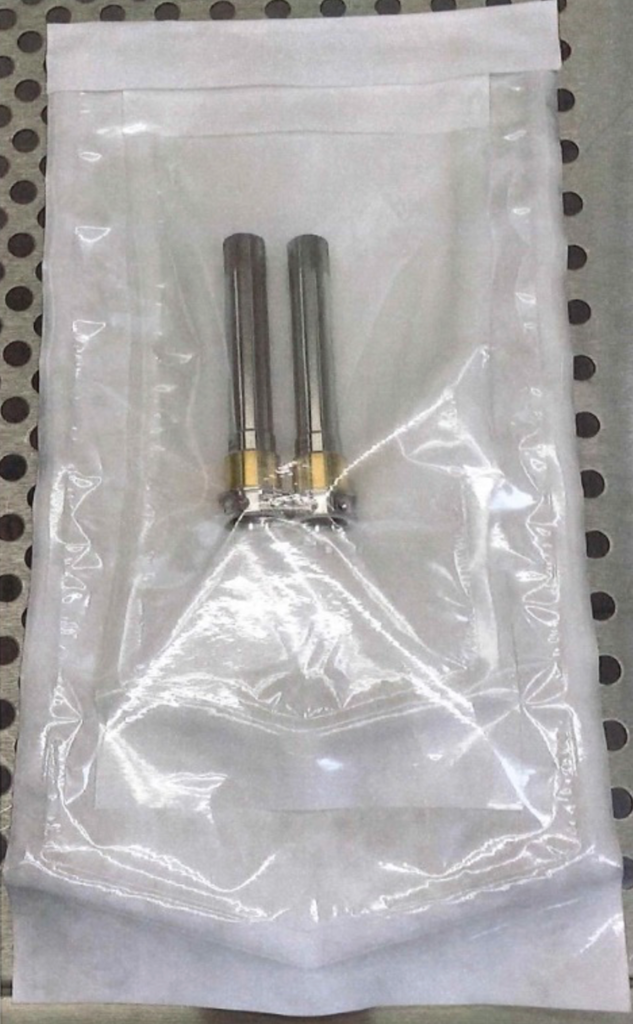
From Analysis to Action: Interventions Unveiled
Armed with insights, we transitioned from analysis to action, focusing on three pillars of intervention:
- Design Interventions: Redesigning equipment to minimize errors, e.g. one example is designing the transfer stopper arm so it cannot be put on the wrong way.
- Procedural Interventions: Enhancing procedures to emphasize critical steps and warnings, e.g. two procedural interventions referred to already include turning an image the correct way and grouping the items to be triple bagged so they are less likely to be forgotten.
- Training Interventions: Developing consistent training aids to ensure skill uniformity, e.g. one example would be to teach people how to tie the bags to make it easier for the staff in the sterile environment.
Each recommendation was tailored to address specific failure modes and performance influencing factors, aiming to mitigate risks and bolster human performance.
These interventions were presented to management, and we could use the risk screening as a communication tool by comparing the current risk scores at the start of the exercise, with the future potential risk scores if the mitigation measures were invested in.
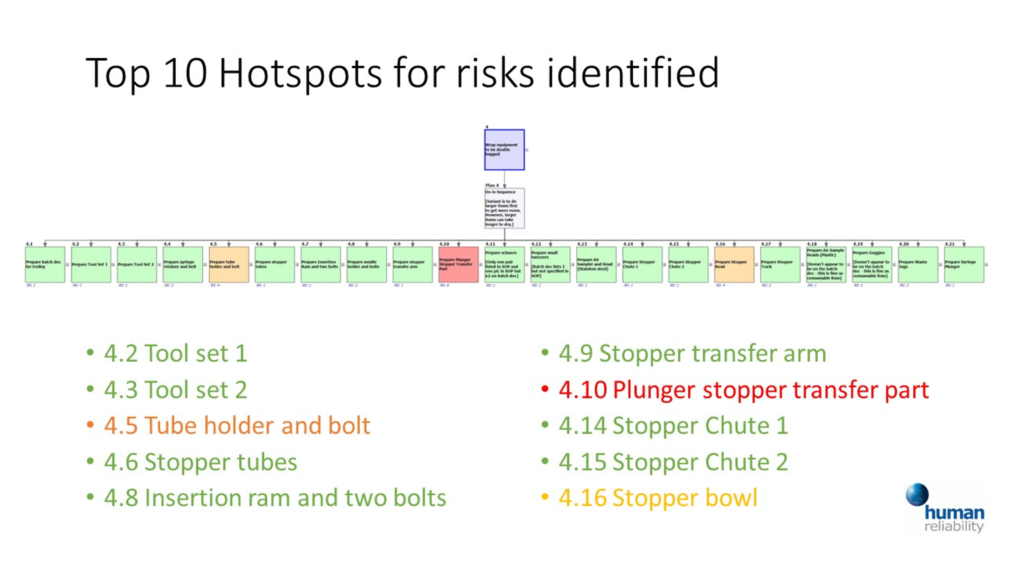
Bridging Proactivity and Reactivity
A pertinent question arises: how do we balance proactive human factors involvement with reactive engagement in industry practice? The answer lies in integrating proactive SCTA methodologies into both design and operational stages. While sectors vary in their adoption, proactive human factors involvement can prevent disasters and foster continuous improvement.
A deviation is any departure from approved processes, procedures, instructions, specifications, or established standards. In the pharmaceutical industry, deviations can occur during drug product development, manufacturing, labelling, packing, sampling, testing, storage, distribution, and other processes.
One of the problems pharmaceutical manufacturers have due to demand outstripping supply, is a tension between fixing a deviation and moving on before the organisation has had time to learn effectively. Essentially, they are in a firefighting mode, trying to keep up with the wave of deviation reports.
If we can get ahead of the game, we can resolve error traps and optimise PIFs reducing the likelihood of the deviations in the first place. Fully switching resource from reactive CAPA management to proactive SCTA would be asking too much, but some investment looking ahead, especially for the organisation’s most critical tasks, might seem a sensible and advantageous approach.
Conclusion: Fostering Risk-Informed Practices
In essence, Systems Critical Task Analysis (SCTA) isn’t just about dissecting tasks; it’s about fostering risk-informed practices and enhancing human performance. The learning from staff, and about their context, is fundamental to this approach. SCTA does this in a structured way and employs techniques to dive deep in areas where it matters. For example, having a well organised and detailed task representation helps staff reflect on those details, having a library of potential failures helps our search for what could go wrong, and exploring system factors that can drive these errors up and down helps us consider sustainable changes. Not having this structure and support might make the meeting more like a brainstorming session! By opening structured dialogues, recognizing vulnerabilities, and implementing targeted interventions, we pave the way for safer, more efficient operations.
So, as we navigate the intricate web of critical tasks, let’s remember the power of systematic analysis and proactive engagement in shaping a safer tomorrow.
Video presentation
We presented this case study to the Institute of Mechanical Engineers (IMechE) on 23rd November 2021. If you’d like to see the full presentation you can do so here:
Find out more
Please get in touch with us to express your interest in a NEW Systems Critical Task Analysis (SCTA) course: https://the.humanreliabilityacademy.com/courses/systems-critical-task-analysis-scta
Have a look at our Systems Critical Task Analysis (SCTA) handbook: SCTA handbook.
Our FREE mini-course the HFCTR mini-course, also provides an introduction to this general approach.
HRA has worked in this area for decades, has a deep history in SHERPA, and we like to consider ourselves as the home of SCTA. If you’re interested in different applications of SCTA have a look at our training and our SHERPA Software toolthat has been developed to help apply the methodology.